Middle-pressure resin bus heat dissipation hole casting mould
A heat-dissipating hole and resin technology, which is applied in the field of heat-dissipating hole molds, can solve the problems of separation of magnetic components from metal casting molds, loss of positioning, and the shape and size of heat-dissipating holes do not meet the requirements, so as to achieve the effect of easy demoulding.
- Summary
- Abstract
- Description
- Claims
- Application Information
AI Technical Summary
Problems solved by technology
Method used
Examples
Embodiment Construction
[0040] The medium-voltage resin busbar cooling hole mold involved in the present invention is as follows: Figure 1~3 As shown, it includes a two-layer structure: an outer elastic jacket 1 and an inner metal mold core 2. The elastic jacket 1 has an inner surface 1a with a slope, and the metal mold core 2 has an outer surface with a corresponding slope. On the surface 2a, the metal mold core 2 supports the elastic jacket 1, so that the external dimensions of the elastic jacket 1 remain unchanged. In this way, the shape and dimension accuracy of the poured cooling holes can be ensured.
[0041] For the convenience of assembly and disassembly, the present invention is also provided with a handle 3 , and the handle 3 is installed through the threaded hole 2 b on the upper part of the metal mold core 2 and the handle screw 4 .
[0042] Such as Figure 4 Shown is the poured medium-voltage resin busbar 5, which includes more than one heat dissipation hole 5a and conductive row 5b. ...
PUM
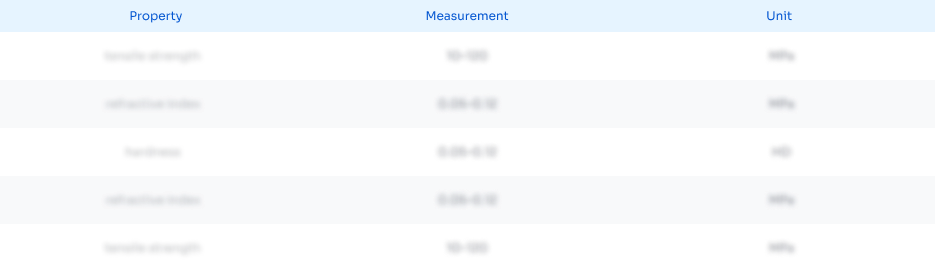
Abstract
Description
Claims
Application Information
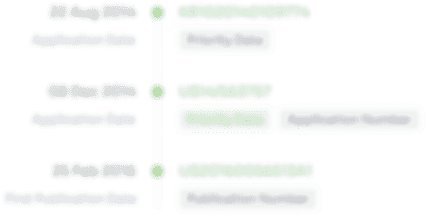
- R&D Engineer
- R&D Manager
- IP Professional
- Industry Leading Data Capabilities
- Powerful AI technology
- Patent DNA Extraction
Browse by: Latest US Patents, China's latest patents, Technical Efficacy Thesaurus, Application Domain, Technology Topic.
© 2024 PatSnap. All rights reserved.Legal|Privacy policy|Modern Slavery Act Transparency Statement|Sitemap