Copper plating process
A process and copper plating technology, applied in the field of copper plating process, can solve the problems of high copper price and high use cost, and achieve the effects of uniform copper plating layer, low use cost and reasonable process
- Summary
- Abstract
- Description
- Claims
- Application Information
AI Technical Summary
Problems solved by technology
Method used
Examples
Example Embodiment
[0007] Example 1
[0008] A copper-plating process, comprising the following steps: 1. Dedusting and degreasing the baseline, 2. Pickling and phosphating, 3. Washing with water, 4. Passivation, 5. Tin plating, immediately cleaning and passivating the baseline into a temperature In the copper plating solution at 20℃~40℃, the transmission speed is controlled at 2~5m / s, and the current density is controlled at 5~15a / dm 2 , 6, wash, 7, dry winding packaging.
[0009] In the copper plating process, the proportion of copper plating solution by mass is: copper hydroxide 10g / L, potassium hydroxide 100g / L, ethylene glycol 100g / L, tripotassium citrate 20g / L and the balance The water is fully stirred and mixed, and the current density is 10 / dm 2 , PH value is 7, temperature is controlled at 40°C.
PUM
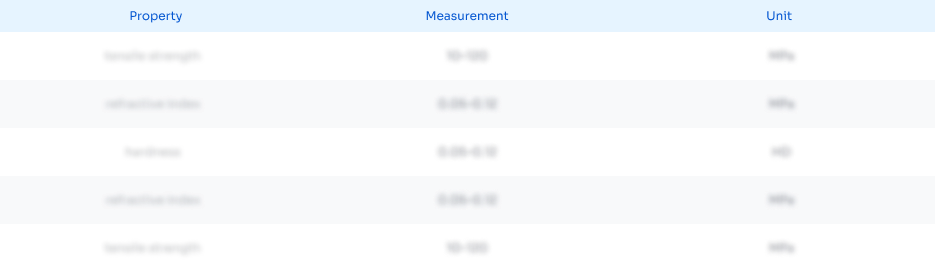
Abstract
Description
Claims
Application Information
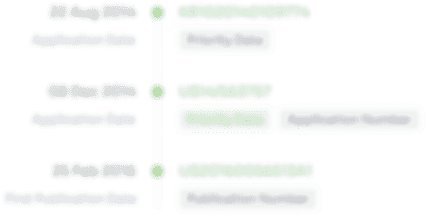
- R&D Engineer
- R&D Manager
- IP Professional
- Industry Leading Data Capabilities
- Powerful AI technology
- Patent DNA Extraction
Browse by: Latest US Patents, China's latest patents, Technical Efficacy Thesaurus, Application Domain, Technology Topic.
© 2024 PatSnap. All rights reserved.Legal|Privacy policy|Modern Slavery Act Transparency Statement|Sitemap