Polypropylene thin film and preparation method thereof
A polypropylene film, polypropylene technology, applied in chemical instruments and methods, flat products, other household appliances, etc., can solve the problems of low production efficiency, polypropylene film cannot have both smoothness, optical properties and mechanical properties. , to achieve the effect of improving production efficiency, reducing friction coefficient and good overall performance
- Summary
- Abstract
- Description
- Claims
- Application Information
AI Technical Summary
Benefits of technology
Problems solved by technology
Method used
Image
Examples
preparation example Construction
[0017]The preparation method of the polypropylene film provided by the present invention comprises mixing polypropylene and self-lubricating microparticles uniformly, feeding them into an extruder for melting and kneading, extruding and granulating to obtain a raw material for a smooth surface layer; The raw material and polypropylene are sent to extrusion casting equipment with a multi-layer co-extrusion structure for extrusion casting to obtain a smooth surface layer comprising a polypropylene core layer and at least one side surface attached to the polypropylene core layer Polypropylene film; the smooth surface layer is a polypropylene layer dispersed with self-lubricating particles; the polypropylene in the polypropylene core layer and the smooth surface layer has a melt index greater than 5g / 10min at 230°C and 2.16kg and less than or equal to 20g / 10min; the self-lubricating particles are polymer particles with a melting temperature greater than or equal to 250°C and a coe
Embodiment 1
[0026] This example is used to illustrate the preparation of the polypropylene film provided by the present invention.
[0027] In this embodiment, the polypropylene forming the polypropylene core layer and the smooth surface layer is purchased from Sinopec Shanghai Petrochemical Co., Ltd., with a melt index of 6 g / 10 minutes at 230 ° C and a temperature of 2.16 kg, and a melting temperature of 156 ° C .
[0028] (1) Preparation of smooth surface layer raw materials:
[0029] The polypropylene is dried in a hot air oven, wherein the drying method is continuous blowing with dry hot air at 80° C. for 8 hours. Add 99.5 parts by weight of dried polypropylene and 0.5 parts by weight of polytetrafluoroethylene particles (particle diameter is 2-4 microns) into the mixer and stir evenly at 25 ° C. The mixer first mixes at a low speed of 100 rpm About 7 minutes, then mix at 200 rpm for 8 minutes at high speed;
[0030] Send the above-mentioned uniformly stirred mixture into a twin-sc
Embodiment 2
[0034] This example is used to illustrate the preparation of the polypropylene film provided by the present invention.
[0035] In this embodiment, the polypropylene core layer and the smooth surface layer are purchased from Singapore TPC Company, with a melt index of 20 g / 10 minutes and a melting temperature of 146° C. at 230° C. and 2.16 kg.
[0036] (1) Preparation of smooth surface layer raw materials:
[0037] The polypropylene is dried in a hot air oven, wherein the drying method is continuous blowing with dry hot air at 80° C. for 8 hours. Add 97 parts by weight of dried polypropylene and 3 parts by weight of polytetrafluoroethylene particles (with a particle diameter of 5-10 microns) into a mixer and stir evenly at 25°C. The mixer first mixes at a low speed of 120 rpm About 5 minutes, then mix at 180 rpm for 6 minutes at high speed;
[0038] Send the above-mentioned uniformly stirred mixture into a twin-screw extruder, adjust the screw speed to 150 rpm, and control th
PUM
Property | Measurement | Unit |
---|---|---|
Melt index | aaaaa | aaaaa |
Melting temperature | aaaaa | aaaaa |
Thickness | aaaaa | aaaaa |
Abstract
Description
Claims
Application Information
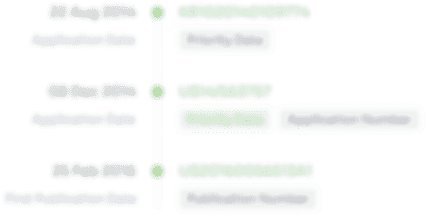
- R&D Engineer
- R&D Manager
- IP Professional
- Industry Leading Data Capabilities
- Powerful AI technology
- Patent DNA Extraction
Browse by: Latest US Patents, China's latest patents, Technical Efficacy Thesaurus, Application Domain, Technology Topic.
© 2024 PatSnap. All rights reserved.Legal|Privacy policy|Modern Slavery Act Transparency Statement|Sitemap