Short-flow preparation method of rare earth doped modified ammonium paratungstate powder
A kind of ammonium paratungstate, rare earth doping technology, applied in chemical instruments and methods, tungsten compounds, inorganic chemistry, etc., can solve the problems of APT particle size is not uniform, lengthy process, labor-intensive, etc., to inhibit the growth of APT particles, shorten Process flow, the effect of reducing labor intensity
- Summary
- Abstract
- Description
- Claims
- Application Information
AI Technical Summary
Problems solved by technology
Method used
Examples
Example Embodiment
[0037] Example 1
[0038] Put 300g of scheelite concentrate powder, 0.7g of yttrium nitrate powder, and 0.7g of lanthanum nitrate powder into a planetary ball mill for wet grinding for 4 hours, put it into a boat, and put the boat into a vacuum drying box at 80 °C for heating and drying for 2 hours. Put the mixed powder into the polytetrafluoroethylene reaction kettle, and then pour 338.5ml of hydrochloric acid with a concentration of 31-38% preheated in the constant temperature water bath into the reaction kettle, stir until fully mixed, and tighten the upper cover of the kettle body. Put it into a homogeneous reactor, the temperature of the homogeneous reactor is set to 80 °C, and the reaction time is 1 h. During the reaction process, the mixture is continuously stirred, and the stirring speed is 60 rad / min. After the reaction is completed, the stirring is stopped, and the residual temperature is used to make The solution was allowed to stand for 0.5h at not lower than 60°C,
Example Embodiment
[0039] Example 2
[0040] Put 300g of scheelite concentrate powder, 6.8g of yttrium nitrate powder, and 34.1g of lanthanum nitrate powder into a planetary ball mill for wet grinding for 6 hours, put them into a boat, and put the boat into a vacuum drying box at 90 °C for heating and drying for 3 hours. Put the mixed powder into the polytetrafluoroethylene reaction kettle, then pour 300ml of preheated concentrated hydrochloric acid in the constant temperature water bath into the reaction kettle, stir until fully mixed, tighten the upper cover of the kettle body, and put it into the homogeneous reactor, The temperature of the homogeneous reactor was set to 90°C, and the reaction time was 2h. During the reaction, the mixture was continuously stirred, and the stirring speed was 70 rad / min. After the reaction was completed, the stirring was stopped, and the residual temperature was used to make the solution no lower than 60°C. Let stand for 2 hours, discard the upper layer waste liq
Example Embodiment
[0041] Example 3
[0042] Put 300g of scheelite concentrate powder, 5.5g of yttrium nitrate powder and 6.2g of lanthanum nitrate powder into a planetary ball mill for wet grinding for 12 hours, put them into a boat, put the boat into a vacuum drying box and heat and dry at 100 °C for 4 hours. Put the mixed powder into the polytetrafluoroethylene reaction kettle, then pour 389.5ml of preheated concentrated hydrochloric acid in the constant temperature water bath into the reaction kettle, stir until fully mixed, tighten the upper cover of the kettle body, and put it into the homogeneous reactor , the temperature of the homogeneous reactor is set to 120 ° C, the reaction time is 3 h, the mixture is continuously stirred during the reaction, and the stirring speed is 70 rad / min. Let stand at ℃ for 2h, pour out the upper layer waste liquid, pour the obtained crude tungstic acid into a polytetrafluoroethylene reaction kettle, add 1503.3ml of ammonia water with a concentration of 28.0-
PUM
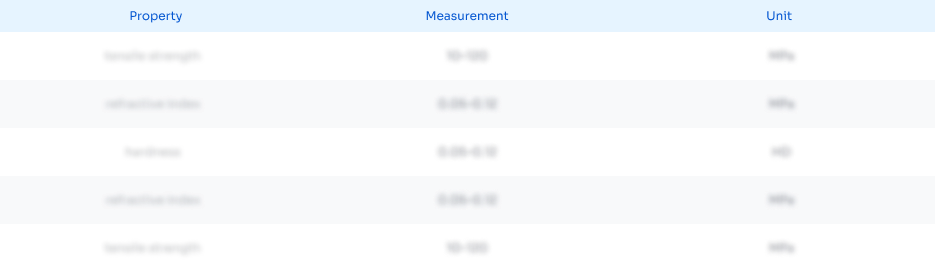
Abstract
Description
Claims
Application Information
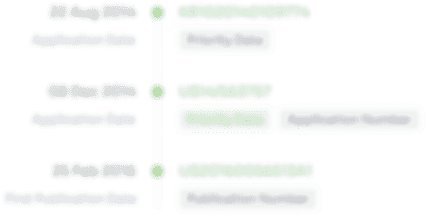
- R&D Engineer
- R&D Manager
- IP Professional
- Industry Leading Data Capabilities
- Powerful AI technology
- Patent DNA Extraction
Browse by: Latest US Patents, China's latest patents, Technical Efficacy Thesaurus, Application Domain, Technology Topic.
© 2024 PatSnap. All rights reserved.Legal|Privacy policy|Modern Slavery Act Transparency Statement|Sitemap