Preparation method of silicon carbide microcrystalline homogenized in dimension and shaped in polyhedron form
A technology of polyhedron and silicon carbide, which is applied in the field of preparation of silicon carbide microcrystals, can solve problems such as difficulty in obtaining, achieve uniform size, and realize the effect of uniform spontaneous nucleation
- Summary
- Abstract
- Description
- Claims
- Application Information
AI Technical Summary
Benefits of technology
Problems solved by technology
Method used
Examples
Embodiment 1
[0024] Put the SiC bulk crystal and the crucible with the microcrystal deposition collector fixed into the crystal growth furnace. Vacuum the crystal growth system to 10 -3 After Pa, after rushing into 15000Pa hydrogen, raise the temperature of the system so that the raw material has a high evaporation temperature (1950-2000°C), and the collector has a relatively low temperature (1950°C), and SiC microcrystal growth is carried out. After 30 minutes of growth , turn off the power supply of the crystal growth furnace, and the product is cooled to room temperature with the furnace. The SiC microcrystalline product attached to the collector was taken out for morphology observation. The grown SiC crystallites are uniform in size (40-50 microns), without agglomeration, and the SiC crystallites present polyhedral morphology.
Embodiment 2
[0026] Put the silicon carbide abrasive and the crucible holding the crystallite deposition collector into the crystal growth furnace. Vacuum the crystal growth system to 3×10 -3 Pa, after filling in 8000Pa hydrogen and argon mixed gas, raise the temperature of the system so that the raw material has a high evaporation temperature (1850-1900°C), and the collector has a relatively low temperature (1800°C), to carry out SiC microcrystalline growth, After 1 hour of growth, the power of the crystal growth furnace was turned off, and the product was cooled to room temperature with the furnace. The SiC microcrystalline product attached to the collector was taken out for morphology observation. The grown SiC crystallites are uniform in size (30-40 microns), without agglomeration, and the SiC crystallites present polyhedral morphology.
Embodiment 3
[0028] Put the mixed powder of Si and C and the crucible fixed with the microcrystal deposition collector into the crystal growth furnace. Vacuum the crystal growth system to 10 -3 Pa, then fill in 10Pa argon, raise the temperature of the system so that the raw material has a high evaporation temperature (1800-1850°C), and the collector has a relatively low temperature (1750°C), for SiC microcrystal growth, after 2 hours of growth , turn off the power supply of the crystal growth furnace, and the product is cooled to room temperature with the furnace. The SiC microcrystalline product attached to the collector was taken out for morphology observation. The grown SiC crystallites have a uniform size (10-20 microns), basically no agglomeration phenomenon, and the SiC crystallites present polyhedral morphology.
PUM
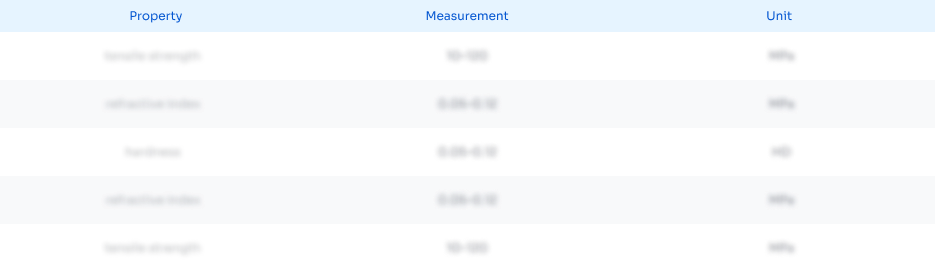
Abstract
Description
Claims
Application Information
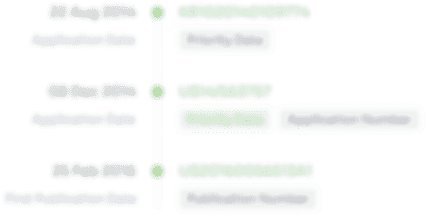
- R&D Engineer
- R&D Manager
- IP Professional
- Industry Leading Data Capabilities
- Powerful AI technology
- Patent DNA Extraction
Browse by: Latest US Patents, China's latest patents, Technical Efficacy Thesaurus, Application Domain, Technology Topic.
© 2024 PatSnap. All rights reserved.Legal|Privacy policy|Modern Slavery Act Transparency Statement|Sitemap