Method of manufacturing silicon carbide-containing heat storage material from waste silicon sludge
A technology of heat storage material and manufacturing method, applied in the direction of manufacturing tools, applications, heat storage equipment, etc., can solve the problems of high production cost, heat storage layer does not have thermal conductivity, heat accumulation characteristics and chemical resistance, etc., to achieve low cost effect
- Summary
- Abstract
- Description
- Claims
- Application Information
AI Technical Summary
Problems solved by technology
Method used
Image
Examples
Example Embodiment
[0054] Implementation
Example Embodiment
[0055] Example 1: Preparation of sintered silicon carbide body
[0056] Centrifuge the silicon sludge obtained from domestic semiconductor wafer manufacturing plants to recover silicon. The above Table 1 shows the components of the impurities contained in the solid of the obtained silicon sludge, that is, the silicon sludge contains not only silicon (Si) but also impurities. Subsequently, the obtained silicon sludge was heat-treated in a reducing atmosphere at a temperature of 300° C. for 120 minutes to remove oil on the obtained silicon sludge. As a result, the remaining oil content in the silicon mud was 5 weight percent.
[0057] Subsequently, the silicon sludge was mixed with carbon black (manufactured by Korea Carbon Black Co., Ltd.) having a particle size of 1 μm to form a pellet parison. In this case, the molar ratio of carbon black to silicon is 1:1.
[0058] In a vacuum atmosphere, the blank was sintered at 1,350°C, 1650°C, 1750°C, and 1850°C for 1 hour. In this case, the
Example Embodiment
[0064] Example 2: Preparation of silicon carbide powder
[0065] The solid of silicon sludge obtained in the same method as in Example 1 was mixed with a carbon source, and then heat-treated at a temperature of 1450°C to 1850°C for 1 hour. In this case, the heat treatment temperature is increased at a rate of 10°C / min. The silicon carbide (SiC) powder was prepared according to the same method as in Example 1, except that the silicon carbide powder was not formed into a small ball shape.
[0066] An electron microscope was used to photograph the appearance of the silicon carbide (SiC) powder prepared in this way.
[0067] Figure 4 A to Figure 4 D shows the electron micrograph of the silicon carbide powder sample heat-treated at 1450°C, 1650°C, 1750°C and 1850°C, Figure 5 It is a graph showing the results of XRD analysis of silicon carbide (SiC) powder prepared at 1450°C.
[0068] From Figure 5 It can be seen that β-SiC powder has been formed (KICET5:5 in the picture). "Marktech"
PUM
Property | Measurement | Unit |
---|---|---|
Particle size | aaaaa | aaaaa |
Abstract
Description
Claims
Application Information
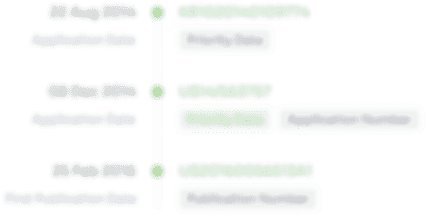
- R&D Engineer
- R&D Manager
- IP Professional
- Industry Leading Data Capabilities
- Powerful AI technology
- Patent DNA Extraction
Browse by: Latest US Patents, China's latest patents, Technical Efficacy Thesaurus, Application Domain, Technology Topic.
© 2024 PatSnap. All rights reserved.Legal|Privacy policy|Modern Slavery Act Transparency Statement|Sitemap