Rolling bearing and associated mounting method
A rolling bearing and mounting surface technology, applied in shaft installation, roller bearings, bearing assembly, etc., can solve a large number of operations, reduce axial and radial forces and other problems, and achieve high mechanical strength
- Summary
- Abstract
- Description
- Claims
- Application Information
AI Technical Summary
Problems solved by technology
Method used
Image
Examples
Example Embodiment
[0020] in figure 1 Medium and large-diameter rolling bearings 10 can be used especially for wind turbines or tunnel drilling rigs. The rolling bearing 10 has a shaft 12, including an inner ring 14, an outer ring 16, and two rows of angular contact rollers 18, 20 placed between the rings. The inner ring 14 and the outer ring 16 are coaxial and extend axially along the axis of rotation 12 of the bearing. The inner ring 14 is an integral ring. The term "integral ring" refers to a ring whose shape is obtained by machining, removing (turning, straightening) chips from pipes, bars, forging and / or rolling stocks. As will be explained in more detail below, the outer ring 16 is specially designed to facilitate the installation of the rollers 18, 20 in the radially defined annular space between the rings.
[0021] The rollers 18, 20 of the bearing are the same themselves, and each roller includes an outer rolling surface 18a, 20a and two opposite end surfaces 18b, 18c, 20b, 20c, which co
PUM
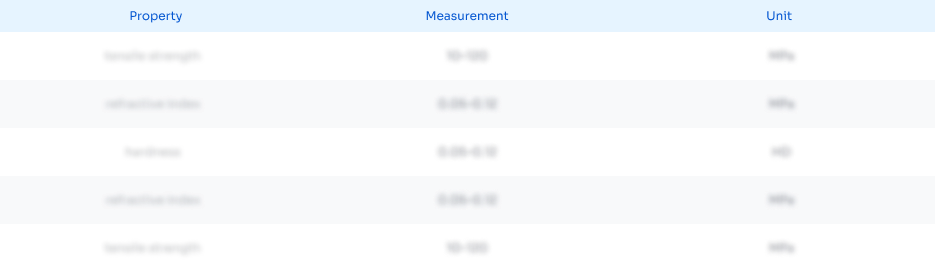
Abstract
Description
Claims
Application Information
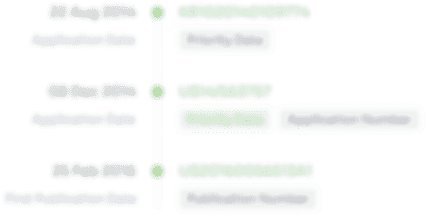
- R&D Engineer
- R&D Manager
- IP Professional
- Industry Leading Data Capabilities
- Powerful AI technology
- Patent DNA Extraction
Browse by: Latest US Patents, China's latest patents, Technical Efficacy Thesaurus, Application Domain, Technology Topic.
© 2024 PatSnap. All rights reserved.Legal|Privacy policy|Modern Slavery Act Transparency Statement|Sitemap