Improved welding mold for welding semiconductor power module
A technology of power modules and semiconductors, which is applied in the direction of semiconductor devices, welding equipment, auxiliary welding equipment, etc., can solve the problems of easy sliding, batch scrapping, etc., achieve the effect of less increase, less number of parts and cost, and guaranteed welding quality
- Summary
- Abstract
- Description
- Claims
- Application Information
AI Technical Summary
Benefits of technology
Problems solved by technology
Method used
Image
Examples
Embodiment Construction
[0009] The invention provides an improved welding mold for welding semiconductor power modules. Describe below in conjunction with accompanying drawing.
[0010] figure 2 Shown is a schematic diagram of the improved welding mold structure. Vertically fix the uprights 9 at both ends or the periphery of the lengthened welding mold base 1, the uprights must be arranged symmetrically; the lower end of each upright 9 is first put on the backing ring 16, the backing ring 16 upper end is covered with the lower pressing plate 10, and the lower spring 13 is pressed Press the lower pressing plate 10, the upper pressing plate 11 presses the lower spring 13, the upper pressing plate 11 presses the upper spring 12, and the adjusting nut 17 is screwed on the upper end of each column 9; adjust the pressure of the upper and lower springs; the other of the upper and lower pressing plates One end presses the electrode positioning plate 6 and the chip positioning sheet 4 respectively, and welds
PUM
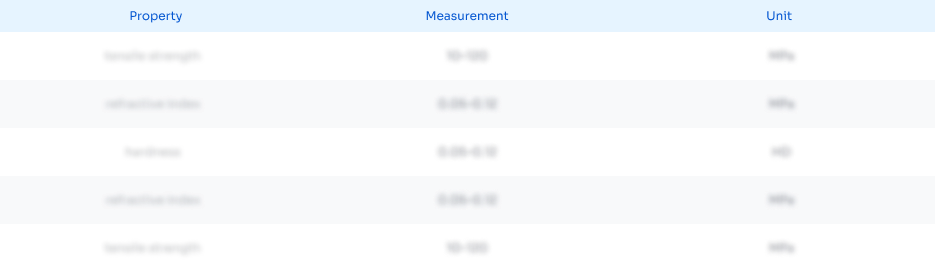
Abstract
Description
Claims
Application Information
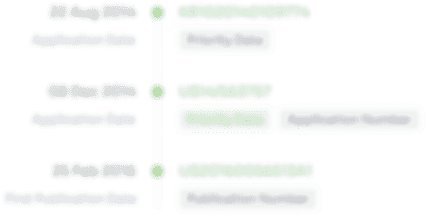
- R&D Engineer
- R&D Manager
- IP Professional
- Industry Leading Data Capabilities
- Powerful AI technology
- Patent DNA Extraction
Browse by: Latest US Patents, China's latest patents, Technical Efficacy Thesaurus, Application Domain, Technology Topic.
© 2024 PatSnap. All rights reserved.Legal|Privacy policy|Modern Slavery Act Transparency Statement|Sitemap