Drilling pump used for drilling
A drilling pump and drilling technology, which is applied in the direction of pumps, piston pumps, liquid displacement machinery, etc., can solve the problems of more restrictions in the production process, cumbersome overall layout, and long production cycle, and achieve simplified power transmission system and simplified structure , The effect of reducing production costs
- Summary
- Abstract
- Description
- Claims
- Application Information
AI Technical Summary
Benefits of technology
Problems solved by technology
Method used
Image
Examples
Embodiment 1
[0015] Example 1, such as figure 1 , figure 2 As shown, a drilling pump for drilling includes a pump body and a power unit, the pump body is fixed on the base 12, the pump body includes a frame assembly 1, a power end assembly 2 and a hydraulic end assembly 3, and the power end assembly Cheng 2 has an eccentric shaft 4, and the power input end of the eccentric shaft 4 is directly connected with the power output end of the power device.
[0016] Such as figure 2 As shown, the power device includes a power source 5, a speed reducer 7, a clutch 6 and a cardan shaft 8, a clutch 6 is connected between the power source 5 and the clutch input end, a cardan shaft 8 is connected to the output end of the clutch 7, and the speed reducer 7 It is a two-stage transmission gearbox.
[0017] Such as image 3 As shown, the eccentric shaft 4 is composed of a stepped shaft 4a and three eccentric blocks 4b fixedly connected with the stepped shaft 4a. The power input end of the eccentric shaft
Embodiment 2
[0019] In Embodiment 2, the eccentric shaft 4 of the drilling pump is an integral structure with three bell cranks obtained by forging, and the other structures of the drilling pump are the same as in Embodiment 1.
PUM
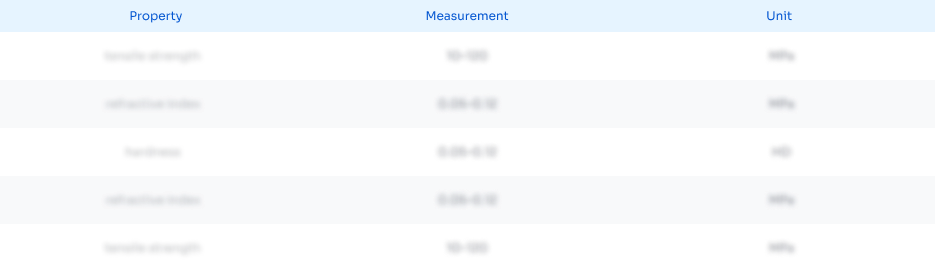
Abstract
Description
Claims
Application Information
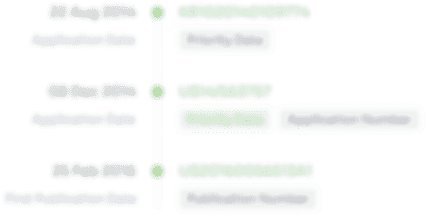
- R&D Engineer
- R&D Manager
- IP Professional
- Industry Leading Data Capabilities
- Powerful AI technology
- Patent DNA Extraction
Browse by: Latest US Patents, China's latest patents, Technical Efficacy Thesaurus, Application Domain, Technology Topic.
© 2024 PatSnap. All rights reserved.Legal|Privacy policy|Modern Slavery Act Transparency Statement|Sitemap