Double-layer structure flexible finishing material and preparation method thereof
A flexible veneer, double-layer structure technology, applied in building construction, covering/lining, construction, etc., to achieve the effect of preventing shedding, simple process and low cost
- Summary
- Abstract
- Description
- Claims
- Application Information
AI Technical Summary
Problems solved by technology
Method used
Examples
Example Embodiment
[0028] Example 1.
[0029] Step 1: In parts by mass, add 8.5 parts of pure acrylic emulsion into 14 parts of water, fully stir and disperse evenly, and add 75 parts of modified fly ash, 2-hydroxy-4-methoxydi 0.1 part of benzophenone-5-sulfonic acid, 2 parts of aluminum hydroxide, 0.1 part of polypropylene staple fibers with a length of 3 mm, and 0.3 part of antifoaming agent, and after stirring evenly, a batching material 1 is obtained, which is for later use.
[0030] Step 2: The batch material 1 obtained in step 1 is pressed and formed in a rolling forming machine to obtain a base layer embryo body of a flexible facing material with a thickness of 1.5 mm, which is dried and dehydrated at 50 degrees Celsius to obtain a flexible facing Material base layer.
[0031] Step 3: In parts by mass, add 2 parts of pure acrylic emulsion to 15 parts of water, fully stir and disperse evenly, and then add 25 parts of Portland cement, 10 parts of fly ash, 0.5 parts of bentonite, 0.05 part of
Example Embodiment
[0034] Example 2.
[0035] Step 1: In parts by mass, add 9 parts of silicone-acrylic emulsion to 15 parts of water, stir and disperse evenly, and then add 72 parts of modified silica fume powder, 2-hydroxy-4-methoxydicarbonate 0.2 part of benzophenone-5-sulfonic acid, 3 parts of magnesium hydroxide, 0.4 part of 5 mm polypropylene staple fiber, 0.4 part of defoamer, and after stirring evenly, a batching material 1 is obtained, which is used for later use.
[0036] Step 2: The batch material 1 obtained in step 1 is pressed and formed in a rolling forming machine to obtain a base layer embryo body of a flexible facing material with a thickness of 2.5 mm, which is dried and dehydrated at 55 degrees Celsius to obtain a flexible facing Material base layer.
[0037] Step 3: In parts by mass, add 3 parts of styrene-acrylic emulsion to 18 parts of water, fully stir and disperse evenly, and then add 27 parts of lime, 8 parts of silica fume, 0.8 parts of bentonite, and water reducing agent
Example Embodiment
[0040] Example 3.
[0041] Step 1: In parts by mass, add 10 parts of styrene-acrylic emulsion to 12 parts of water, fully stir and disperse evenly, and then add 75 parts of modified fly ash, 2-hydroxy-4-methoxy di 0.2 part of benzophenone-5-sulfonic acid, 2 parts of aluminum hydroxide, 0.3 part of 4 mm glass fiber, and 0.5 part of defoaming agent are mixed to obtain batching material 1, which is for later use.
[0042] Step 2: Press and shape the batch material 1 prepared in the step 1 in a roll forming machine to obtain a base layer embryo body of a flexible facing material with a thickness of 5 mm, which is dried and dehydrated at 60 degrees Celsius to obtain a flexible facing Material base layer.
[0043]Step 3: In parts by mass, add 2.5 parts of pure acrylic emulsion to 20 parts of water, fully stir and disperse evenly, and then add 30 parts of alkali-activated gelling material, 9 parts of fly ash, and 0.8 parts of montmorillonite in sequence. 0.1 part of water reducing age
PUM
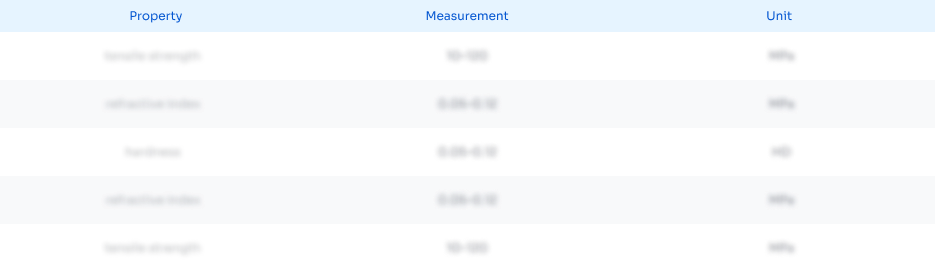
Abstract
Description
Claims
Application Information
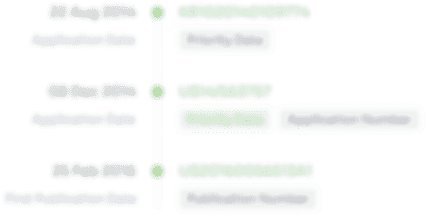
- R&D Engineer
- R&D Manager
- IP Professional
- Industry Leading Data Capabilities
- Powerful AI technology
- Patent DNA Extraction
Browse by: Latest US Patents, China's latest patents, Technical Efficacy Thesaurus, Application Domain, Technology Topic.
© 2024 PatSnap. All rights reserved.Legal|Privacy policy|Modern Slavery Act Transparency Statement|Sitemap