Manufacturing method for high-speed permanent magnetic rotor
A permanent magnet rotor and manufacturing method technology, applied in the manufacture of stator/rotor body, etc., can solve problems such as potential safety hazards, and achieve the effect of meeting the requirements of high-speed use
- Summary
- Abstract
- Description
- Claims
- Application Information
AI Technical Summary
Benefits of technology
Problems solved by technology
Method used
Image
Examples
Embodiment Construction
[0016] As shown in the figure, the manufacturing method of the high-speed permanent magnet rotor includes the following steps:
[0017] (1) Processing: Process the permanent magnet pole 2, left baffle plate 4, right baffle plate 5, rotor core 1, and thin-walled sheath 3 to the requirements of the drawing, among which the permanent magnet pole 2 is a sintered permanent magnet pole ;
[0018] (2) Install the left baffle: press-fit the left baffle 4 onto the rotor core 1, the press-fit interference is between 0.04mm and 0.05mm, and then follow the requirements of the C-level standard in GB / T22085.2 Laser welding the two into one;
[0019] (3) Install the magnetic poles: use TS812 high-temperature structural adhesive to pair the magnetic poles according to different polarities, and bond the counterweight to the rotor core 1, and fill the gap with TS812 high-temperature structural adhesive and then cure. The curing time is 32 to 40 hours;
[0020] (4) Install the right baffle plat
PUM
Property | Measurement | Unit |
---|---|---|
Weld width | aaaaa | aaaaa |
Depth | aaaaa | aaaaa |
Thickness | aaaaa | aaaaa |
Abstract
Description
Claims
Application Information
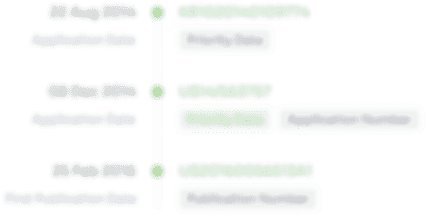
- R&D Engineer
- R&D Manager
- IP Professional
- Industry Leading Data Capabilities
- Powerful AI technology
- Patent DNA Extraction
Browse by: Latest US Patents, China's latest patents, Technical Efficacy Thesaurus, Application Domain, Technology Topic.
© 2024 PatSnap. All rights reserved.Legal|Privacy policy|Modern Slavery Act Transparency Statement|Sitemap