Sized phase change material and preparation method thereof
A technology of phase change materials and raw materials, applied in heat exchange materials, chemical instruments and methods, etc., can solve the problems of low thermal stability, easy to produce plastic crystals, poor thermal conductivity, etc., and achieve good thermal stability and high thermal conductivity. , the effect of excellent performance
- Summary
- Abstract
- Description
- Claims
- Application Information
AI Technical Summary
Benefits of technology
Problems solved by technology
Method used
Image
Examples
Embodiment 1
[0027] A preparation method for a shaped phase change material, comprising the steps of:
[0028] 1) Preparation of rare earth oxide modified solid-solid phase change materials (or modified solid-solid phase change materials):
[0029] ①After drying the analytically pure trimethylolethane, grind it into a uniform powder, pass through a 200-mesh sieve, put it in a drying dish for 24 hours and take it out (the purpose is to fully dry the raw material and discharge the internal gas to ensure its No air bubbles are generated during use), ready for use;
[0030] 2. again according to the mass percentage of each raw material: trimethylolethane 95%, neodymium oxide 5%, select trimethylolethane and neodymium oxide;
[0031] ③ Mechanically blend trimethylolethane and neodymium oxide powder for 12 hours, and after mixing evenly, obtain a solid-solid phase change material modified by rare earth oxides;
[0032]2) According to the mass percentage of each raw material: rare earth oxide modi
Embodiment 2
[0038] A preparation method for a shaped phase change material, comprising the steps of:
[0039] 1) Preparation of solid-solid phase change materials modified by rare earth oxides:
[0040] ①After drying the analytically pure trimethylolethane, grind it into a uniform powder, pass through a 200-mesh sieve, put it in a drying dish for 24 hours and take it out (the purpose is to fully dry the raw material and discharge the internal gas to ensure its use No air bubbles will be generated during the time), stand-by;
[0041] ②According to the mass percentages of each raw material: trimethylolethane 90%, neodymium oxide 10%, select trimethylolethane and neodymium oxide;
[0042] ③ Mechanically blend trimethylolethane and neodymium oxide powder for 12 hours, and after mixing evenly, obtain a solid-solid phase change material modified by rare earth oxides;
[0043] 2) According to the mass percentage of each raw material: rare earth oxide modified solid-solid phase change material 80%
Embodiment 3
[0048] A preparation method for a shaped phase change material, comprising the steps of:
[0049] 1) Preparation of solid-solid phase change materials modified by rare earth oxides:
[0050] ① First dry the analytically pure trimethylolethane and grind them into uniform powder, pass through a 200-mesh sieve, put it in a drying dish for 24 hours and take it out (the purpose is to fully dry the raw materials and discharge the internal gas to ensure its use No air bubbles will be generated during the time), stand-by;
[0051] ②According to the mass percentages of each raw material: trimethylolethane 92%, yttrium oxide 3%, neodymium oxide 5%, select trimethylolethane, yttrium oxide and neodymium oxide;
[0052] ③Then mechanically blend trimethylolethane, yttrium oxide and neodymium oxide powder for 12 hours, and after mixing evenly, a solid-solid phase change material modified by rare earth oxide is obtained;
[0053] 2) According to the mass percentage of each raw material: rare e
PUM
Property | Measurement | Unit |
---|---|---|
Phase transition temperature | aaaaa | aaaaa |
Phase change enthalpy | aaaaa | aaaaa |
Phase change enthalpy | aaaaa | aaaaa |
Abstract
Description
Claims
Application Information
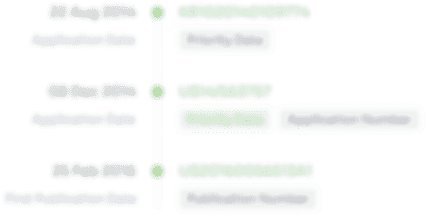
- R&D Engineer
- R&D Manager
- IP Professional
- Industry Leading Data Capabilities
- Powerful AI technology
- Patent DNA Extraction
Browse by: Latest US Patents, China's latest patents, Technical Efficacy Thesaurus, Application Domain, Technology Topic.
© 2024 PatSnap. All rights reserved.Legal|Privacy policy|Modern Slavery Act Transparency Statement|Sitemap