Oil injector forming process
A molding process and fuel injector technology, applied in the direction of metal processing equipment, etc., can solve the problems that the internal structure and grain cannot fully meet the performance requirements, blanking and flash can not be reused, and the surface of the fixture mold can be reduced. Effects of secondary surface damage, material cost saving, scale reduction
- Summary
- Abstract
- Description
- Claims
- Application Information
AI Technical Summary
Problems solved by technology
Method used
Examples
Embodiment Construction
[0012] The present invention will be further described in conjunction with examples.
[0013] A molding process of a fuel injector, comprising the following steps:
[0014] (1) Feed the steel plate material into the cold heading machine for shearing, and cold forge the sheared material to forge the pre-forged body of the injector in the shape of a rotary body;
[0015] (2) Put the fuel injector body into the intermediate frequency furnace for heating, and the heating temperature is 800-1000°C;
[0016] (3) Put the pre-forged body of the fuel injector into the die chamber with the injector membrane cavity, and then perform final forging by the press to forge the asymmetric part of the fuel injector;
[0017] (4) Tempering the entire pre-forged body at a tempering temperature of 520-600°C, and then cooling naturally;
[0018] (5) Finally, cut off the flash on the asymmetric part of the injector.
[0019] Preferably, before heating in an intermediate frequency furnace, an anti...
PUM
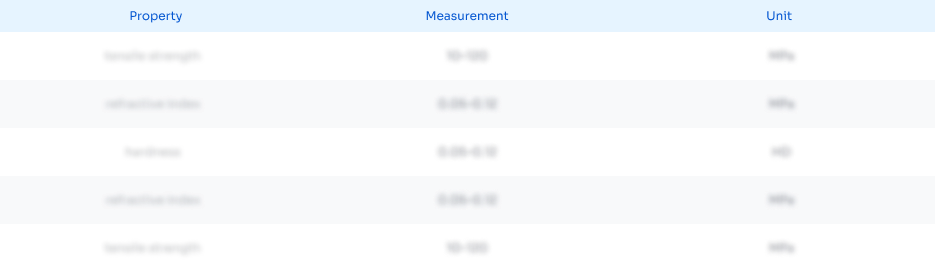
Abstract
Description
Claims
Application Information
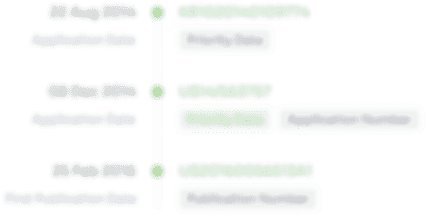
- R&D Engineer
- R&D Manager
- IP Professional
- Industry Leading Data Capabilities
- Powerful AI technology
- Patent DNA Extraction
Browse by: Latest US Patents, China's latest patents, Technical Efficacy Thesaurus, Application Domain, Technology Topic.
© 2024 PatSnap. All rights reserved.Legal|Privacy policy|Modern Slavery Act Transparency Statement|Sitemap