Preparation method for metal/polymer with double-layer nanostructure
A technology of double-layer nanostructure and nano-metal thin film, which is applied in the photolithographic process of patterned surface, photolithographic coating equipment, and optomechanical equipment, etc., which can solve the difficulty of constructing metal/polymer double-layer three-dimensional nanocomposite materials , low structural strength, prone to defects, etc., to achieve the effect of ensuring reusability, stable and reliable quality, and reducing production costs
- Summary
- Abstract
- Description
- Claims
- Application Information
AI Technical Summary
Benefits of technology
Problems solved by technology
Method used
Image
Examples
Embodiment 1
[0061] The preparation method is as follows:
[0062] In the first step, a layer of 1H, 1H, 2H, 2H-perfluorooctyltrichlorosilane is modified on the surface of the template with a three-dimensional conical shape structure and a period of 400 nm by self-assembly method as an anti-sticking layer ;
[0063] On the anti-sticking layer, a layer of nano-silver thin film layer is deposited by magnetron sputtering method; the thickness of the film layer is 20±5nm;
[0064] Then, spin-coat a layer of ultraviolet photoresist on the nano-silver thin film layer to obtain an ultraviolet photoresist thin film layer, and the thickness of the ultraviolet photoresist thin film layer is 500 ± 50nm;
[0065] The second step is to take the quartz plate, stack the quartz plate on the template in the way that the template is on the bottom and the quartz plate is on the top, and assemble it into a sample to be imprinted;
[0066] Open the equipment door of the nano-imprinting machine, place the sample
Embodiment 2
[0084] In addition to using chloroform instead of acetone, the template used is a template with a three-dimensional circular frustum structure with a period of 800nm, and the pressure during the UV imprinting process is 150KPa;
[0085] All the other are the same as in Example 1.
[0086] Product performance testing:
[0087] Detection instrument: scanning electron microscope.
[0088] Detection method: The obtained product is brittle broken with liquid nitrogen, placed on the stage with an inclination of 10°, and observed at a magnification of 60,000 times.
[0089] Test results such as figure 2 Shown: from figure 2 It can be clearly seen that the overall molding effect of the imprinted surface of the composite material is good, showing obvious structural features of the frustum of a cone.
[0090] figure 2 In , the white edge is the (approximately 20 nm thick) metallic silver film, and the interior is the polymer layer.
[0091] from figure 2 , it can also be clearly
Embodiment 3
[0093] In addition to using dichloromethane instead of acetone, the template used is a two-dimensional wave-shaped template with a period of 300nm, and the pressure during the UV imprinting process is 200KPa;
[0094] All the other are the same as in Example 1.
[0095] Product performance testing:
[0096] Detection instrument: scanning electron microscope.
[0097] Detection method: The obtained product is brittle broken with liquid nitrogen, placed on the stage with an inclination of 10°, and observed at a magnification of 45,000 times.
[0098] Test results such as image 3 Shown: from image 3 It can be seen from the upper part that for the preparation of two-dimensional metal / polymer double-layer structure, the effect of this method is more obvious, the overall forming effect of the structure is good, and the outline of the wave structure is very obvious. The white edge of the structure is a 20nm thick metallic silver film, and the interior is a polymer layer.
[009
PUM
Property | Measurement | Unit |
---|---|---|
Thickness | aaaaa | aaaaa |
Thickness | aaaaa | aaaaa |
Abstract
Description
Claims
Application Information
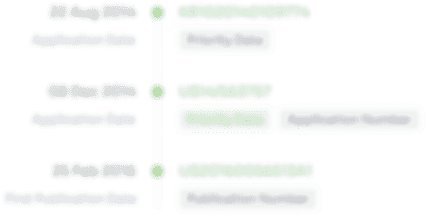
- R&D Engineer
- R&D Manager
- IP Professional
- Industry Leading Data Capabilities
- Powerful AI technology
- Patent DNA Extraction
Browse by: Latest US Patents, China's latest patents, Technical Efficacy Thesaurus, Application Domain, Technology Topic.
© 2024 PatSnap. All rights reserved.Legal|Privacy policy|Modern Slavery Act Transparency Statement|Sitemap