Method for manufacturing integrally-molded composite hat stiffener
A technology of integral molding and composite materials, which is applied in the field of manufacturing new composite hat ribs, can solve the problem of high cost, achieve the effects of reducing consumption, reducing structural weight, and reducing material costs
- Summary
- Abstract
- Description
- Claims
- Application Information
AI Technical Summary
Benefits of technology
Problems solved by technology
Method used
Image
Examples
Embodiment Construction
[0015] Below in conjunction with accompanying drawing and specific embodiment the present invention is described in further detail:
[0016] Depend on figure 1 , figure 2 visible:
[0017] A method for integrally forming a hat rib of a composite material. include
[0018] In the metal mold, PMI (polymethacrylimide) foam 1 is evenly coated with a certain thickness of water-soluble mandrel 2;
[0019] The water-soluble mandrel is compacted by means of vacuum bag pressing;
[0020] Remove moisture in the core mold by heating in an oven, and finally obtain a mold with a water-soluble core mold covered with PMI foam;
[0021] according to figure 2 Laying the carbon fiber fabric prefabricated body 3 in a manner;
[0022] Using VARI (Vacuum Assisted Resin Infusion: Vacuum Assisted Resin Infusion) process for injection and curing;
[0023] Use clear water to wash away the water-soluble mandrel covered by PMI foam to obtain an integrally formed hat rib.
[0024] The invention c
PUM
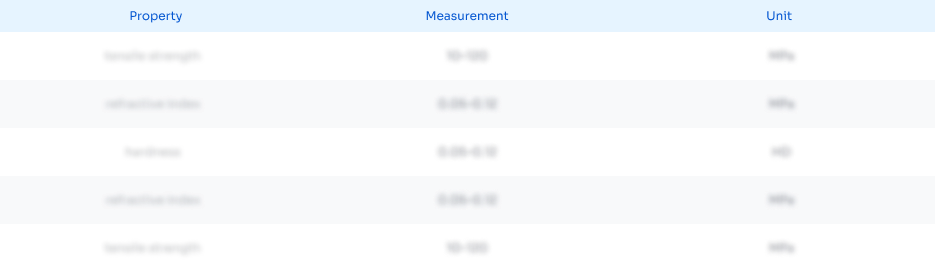
Abstract
Description
Claims
Application Information
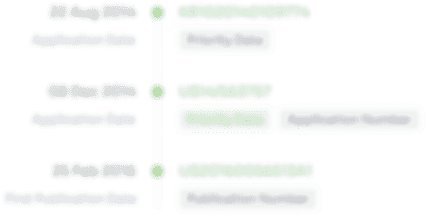
- R&D Engineer
- R&D Manager
- IP Professional
- Industry Leading Data Capabilities
- Powerful AI technology
- Patent DNA Extraction
Browse by: Latest US Patents, China's latest patents, Technical Efficacy Thesaurus, Application Domain, Technology Topic.
© 2024 PatSnap. All rights reserved.Legal|Privacy policy|Modern Slavery Act Transparency Statement|Sitemap