Transmission shaft forging process
A transmission shaft and process technology, applied in the field of forging, can solve the problems of high forging pressure and easy generation of defects, and achieve the effects of improving strength and rigidity, uniform internal deformation and grain refinement
- Summary
- Abstract
- Description
- Claims
- Application Information
AI Technical Summary
Problems solved by technology
Method used
Examples
Embodiment 1
[0006] A transmission shaft forging process, which is characterized in that it includes the following steps: 1) heating the billet steel ingot to 1200°C in the first fire, chamfering the edge, and keeping it warm for 6 hours; 1) The billet obtained in step 1) is upsetting, lengthened, and then naturally cooled to 450°C; 3) For the billet obtained in step 2), heated to a temperature range of 700°C and kept for 3 hours, and then furnace cooled to a temperature range of 320°C And keep it warm for 2 hours, then heat it to a temperature range of 680°C and keep it warm for 18 hours, cool it to 100°C and release it from the furnace; the arc-shaped tooth-shaped anvil with an upper convex and a lower concave includes an upper anvil and a lower anvil, and the upper anvil has two sides Two or more arc convex surfaces of equal radius are set from the conical surface to the middle, and the adjacent arc convex surfaces are smooth and transitional, and the lower anvil is a V-shaped conical surfa
Embodiment 2
[0008] A transmission shaft forging process, which is characterized in that it includes the following steps: 1) heating the blank steel ingot to 1210°C in the first fire, chamfering the edge, and keeping it warm for 6 hours; 1) The billet obtained in step 1) is upsetting, lengthened, and then naturally cooled to 480°C; 3) For the billet obtained in step 2), heated to a temperature range of 710°C and kept for 3.5h, and then furnace cooled to a temperature of 330°C range and keep it warm for 2.5 hours, then heat it up to a temperature range of 690°C and keep it warm for 19 hours, and cool it to 100°C to release from the furnace; the arc-shaped tooth-shaped convex-concave anvil includes an upper anvil and a lower anvil, and the upper anvil is The conical surfaces on both sides protrude to the middle to form two or more convex circular arc convex surfaces of equal radius, and the adjacent circular arc convex surfaces are smooth and transitional, and the lower anvil is a V-shaped conic
Embodiment 3
[0010] A transmission shaft forging process, which is characterized in that it includes the following steps: 1) heating the blank steel ingot to 1220°C in the first fire, chamfering the edge, and keeping it warm for 6 hours; 1) The billet obtained in step 1) is upsetting, lengthened, and then naturally cooled to 500°C; 3) For the billet obtained in step 2), heated to a temperature range of 720°C and kept for 4 hours, and then furnace cooled to a temperature range of 350°C And keep it warm for 3 hours, then heat it to a temperature range of 700°C and hold it for 20 hours, cool it to 100°C and release it from the furnace; the arc-shaped tooth-shaped anvil with an upper convex and a lower concave includes an upper anvil and a lower anvil, and the upper anvil has two sides Two or more arc convex surfaces of equal radius are set from the conical surface to the middle, and the adjacent arc convex surfaces are smooth and transitional, and the lower anvil is a V-shaped conical surface tha
PUM
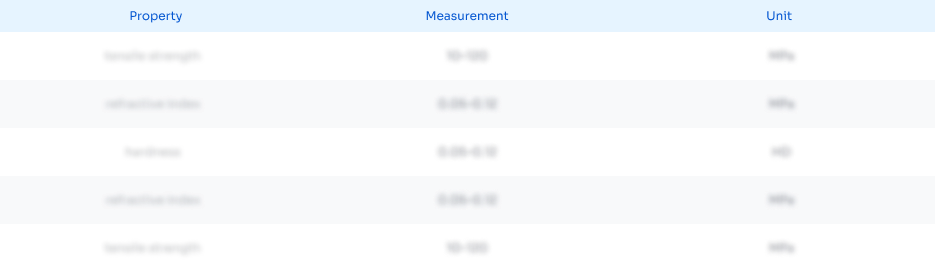
Abstract
Description
Claims
Application Information
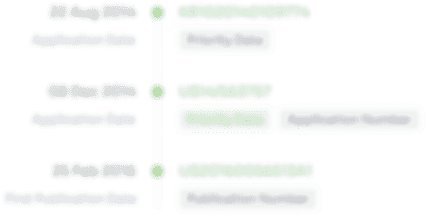
- R&D Engineer
- R&D Manager
- IP Professional
- Industry Leading Data Capabilities
- Powerful AI technology
- Patent DNA Extraction
Browse by: Latest US Patents, China's latest patents, Technical Efficacy Thesaurus, Application Domain, Technology Topic.
© 2024 PatSnap. All rights reserved.Legal|Privacy policy|Modern Slavery Act Transparency Statement|Sitemap