Method for manufacturing bottom shrunk type steel ingot mold
A manufacturing method and technology of steel ingot moulds, which are applied in the field of metallurgical foundry industry, can solve problems such as easy cracks and peeling, waste of process materials, etc., and achieve the effect of convenient operation and ideal practical effect
- Summary
- Abstract
- Description
- Claims
- Application Information
AI Technical Summary
Problems solved by technology
Method used
Image
Examples
Embodiment Construction
[0015] The present invention will be described in detail below in conjunction with the accompanying drawings and embodiments.
[0016] see figure 1 and figure 2 , the present invention provides a bottom-retracting steel ingot mold and a manufacturing method thereof. The bottom of the steel ingot mold 1 is closed, and the inner wall at the bottom 2 of the steel ingot mold is provided with two different sections of reduced caliber and caliber height, and the reduced caliber close to the outer mouth It is a small caliber, the inner side of the small caliber is a reduced large caliber, and the height H of the large caliber is greater than the height h of the small caliber, so as to prevent the closing part from melting too quickly.
[0017] Such as figure 1 As shown in , a smooth transition is formed between the height H of the large diameter and the height h of the small diameter of the inner wall of the bottom 2 of the ingot mold.
[0018] In the case of reducing the diameter o
PUM
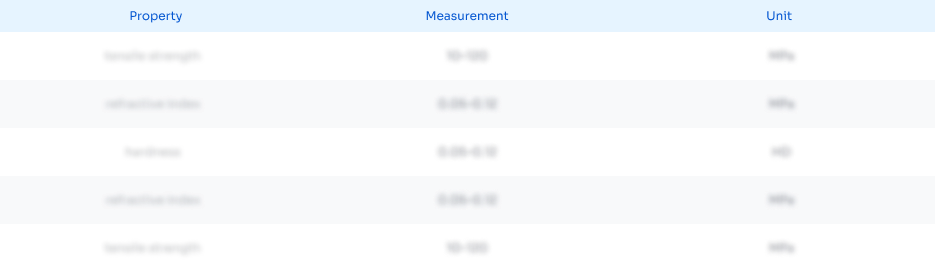
Abstract
Description
Claims
Application Information
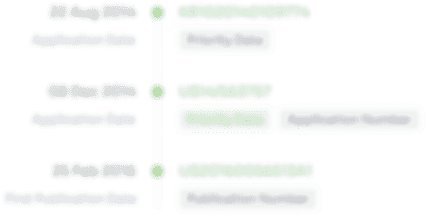
- R&D Engineer
- R&D Manager
- IP Professional
- Industry Leading Data Capabilities
- Powerful AI technology
- Patent DNA Extraction
Browse by: Latest US Patents, China's latest patents, Technical Efficacy Thesaurus, Application Domain, Technology Topic.
© 2024 PatSnap. All rights reserved.Legal|Privacy policy|Modern Slavery Act Transparency Statement|Sitemap