Method for preparing silicon carbide ceramic material with low residual silicon by adopting multi-step reaction sintering method
A technology of silicon carbide ceramics and sintering method, which is applied in the field of silicon carbide ceramics sintering, can solve the problems of high residual silicon content and limitations, and achieve the effect of expanding the scope of application
- Summary
- Abstract
- Description
- Claims
- Application Information
AI Technical Summary
Benefits of technology
Problems solved by technology
Method used
Examples
Embodiment 1
[0028] In this embodiment, a multi-step reaction sintering method is used to prepare a silicon carbide kiln conveyor chain, which specifically includes the following steps:
[0029] The first step is to select nano-carbon black as the carbon source with high activity and petroleum coke as the carbon source with low activity through testing;
[0030] In the second step, mix nano-carbon black, 20wt.% petroleum coke and 48wt.% silicon carbide powder with a mass fraction of 30wt.%, and add a phenolic resin with a mass fraction of 2wt.%. First use wet mixing with a rotation speed of 180r / min, mix the powder for 4h, then dry mix, the speed is 100r / min, mix the powder for 5h;
[0031] The third step is to use the method of compression molding to press the powder, fill the powder evenly into the mold, and use the pressure of 30MPa ~ 60MPa to carry out two-way pressure, and the holding time is 30S;
[0032] The fourth step is to place the green body molded in the third step on the f
Embodiment 2
[0037] In this embodiment, a silicon carbide tube heat exchanger is prepared by reaction sintering, which specifically includes the following steps:
[0038] The first step is to obtain the carbon source activity through X-ray diffraction analysis, and choose petroleum coke, mesocarbon microspheres, and graphite as the added carbon source;
[0039] In the second step, 15wt.% of petroleum coke, 20wt.% of mesophase carbon microspheres, 20wt.% of graphite and 40wt.% of silicon carbide powder were mixed, and 5wt.% of hydroxyethyl cellulose was added. ;Use a planetary ball mill for wet mixing for 4 hours at a speed of 200r / min, and after drying, use a planetary ball mill for dry mixing for 3 hours at a speed of 120r / min;
[0040] The third step is to shape the uniformly mixed raw materials, add water 0.2 times the weight of the powder to the powder, and use extrusion molding to form the green body. The length of the shaping section is 28mm, the extrusion angle is 45o, and the radi
Embodiment 3
[0046] This embodiment adopts the method of reaction sintering to prepare silicon carbide reflective mirror, specifically including the following steps:
[0047] In the first step, Raman spectroscopy and transmission electron microscopy are used to evaluate the activity of carbon sources, and nano-carbon black and graphite are selected as composite carbon sources for addition;
[0048] In the second step, mix nano-carbon black, 20wt.% graphite, and 45wt.% silicon carbide powder with a mass fraction of 25wt.%, and add PVA with a mass fraction of 10wt.%. First use wet mixing with a speed of 180r / min , mixed powder for 4 hours, then dry mixed at a speed of 100r / min, and mixed powder for 5 hours;
[0049] The third step is to use the method of compression molding to press the powder, fill the powder evenly into the mold, and use the pressure of 30MPa ~ 60MPa to carry out two-way pressure, and the holding time is 30S;
[0050] The fourth step is to place the green body molded in
PUM
Property | Measurement | Unit |
---|---|---|
Density | aaaaa | aaaaa |
Bending strength | aaaaa | aaaaa |
Bending strength | aaaaa | aaaaa |
Abstract
Description
Claims
Application Information
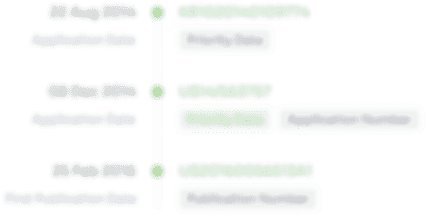
- R&D Engineer
- R&D Manager
- IP Professional
- Industry Leading Data Capabilities
- Powerful AI technology
- Patent DNA Extraction
Browse by: Latest US Patents, China's latest patents, Technical Efficacy Thesaurus, Application Domain, Technology Topic.
© 2024 PatSnap. All rights reserved.Legal|Privacy policy|Modern Slavery Act Transparency Statement|Sitemap