Preparation method of basalt fiberboard spring
A technology of basalt fiber plate and leaf spring, which is applied in the field of preparation of basalt fiber leaf spring, can solve the problems of poor stiffness of leaf spring, complicated process, shortening service life of composite leaf spring, etc., achieves reduced production cost, high stiffness and strength, and extended service life The effect of longevity
- Summary
- Abstract
- Description
- Claims
- Application Information
AI Technical Summary
Problems solved by technology
Method used
Image
Examples
Embodiment Construction
[0017] The present invention will be further described below in conjunction with accompanying drawing, protection scope of the present invention is not limited to the following:
[0018] Such as Figure 1~5 Shown, a kind of preparation method of basalt fiber leaf spring, it may further comprise the steps:
[0019] S1. Establish a three-dimensional model of the leaf spring according to the requirements of the leaf spring;
[0020] S2. To make the upper mold, first take a die A, and then mill the lower surface of the die A to form a cavity 2 that matches the profile of the upper surface of the leaf spring 1, and then mill the two ends of the cavity 2 to form a horizontal A cavity A3 with a semicircular cross-section, and finally process two strip-shaped grooves 6 with variable cross-section at the bottom of the cavity 2, so as to make an upper mold;
[0021] S3. To make the lower mold, first take a die B, then mill the upper surface of the die B to form a boss 4 that matches the
PUM
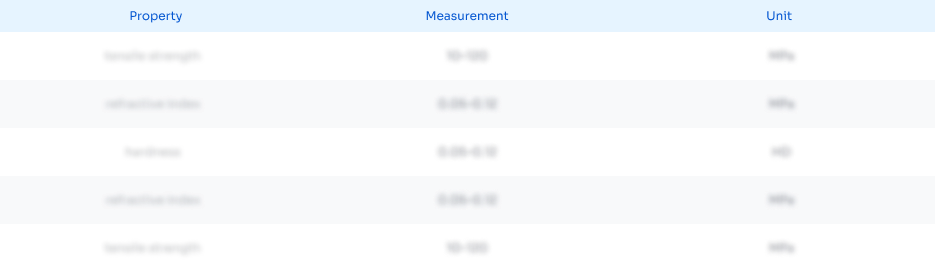
Abstract
Description
Claims
Application Information
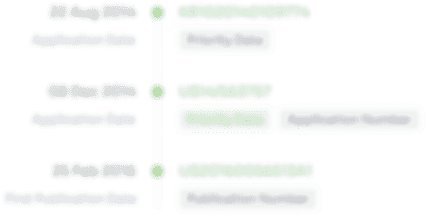
- R&D Engineer
- R&D Manager
- IP Professional
- Industry Leading Data Capabilities
- Powerful AI technology
- Patent DNA Extraction
Browse by: Latest US Patents, China's latest patents, Technical Efficacy Thesaurus, Application Domain, Technology Topic.
© 2024 PatSnap. All rights reserved.Legal|Privacy policy|Modern Slavery Act Transparency Statement|Sitemap