Nylon fabric and printing production technology thereof and application of nylon special heat transfer ink
A technology of nylon fabric and production process, which is applied in the application field of nylon fabric and its printing production process, and nylon special thermal transfer ink, which can solve the problems of affecting product appearance quality, complicated printing process, high production cost, etc., and achieve color migration phenomenon The effect of blocking, excellent printing quality and high color fastness
- Summary
- Abstract
- Description
- Claims
- Application Information
AI Technical Summary
Problems solved by technology
Method used
Examples
Example Embodiment
[0071] Example 1
[0072] A nylon fabric printing production process, comprising the following process steps:
[0073] Step (1) printing the thermal transfer ink on the transfer paper through a digital printing printer;
[0074] Step (2) Transfer the printing pattern to the nylon fabric through the thermal transfer paper, and the operating temperature and time are respectively 180°C and 60s to prepare the nylon printed fabric;
[0075] The thermal transfer ink is composed of the following raw materials by weight: disperse red 118 color paste: 30%, sorbitol: 10%, butanediol: 10%, color fixing agent: 3%, defoaming agent: 0.02% , Surface tension regulator: 0.03%, deionized water: balance.
[0076] Among them, disperse red 118 color paste is composed of the following raw materials by weight: disperse red 86: 21%, sodium lignosulfonate: 17%, polyester dispersing aid: 15%, γ-butyrolactone: 7%, Deionized water: balance, average particle size is 65 nm.
[0077] Wherein, the color-fix
Example Embodiment
[0083] Example 2
[0084] A nylon fabric printing production process, comprising the following process steps:
[0085] Step (1) print the thermal transfer ink on the transfer paper through a digital printer;
[0086] Step (2) The obtained transfer paper is transferred to the nylon fabric through the thermal transfer process, and the operating temperature and time are respectively 190 ° C and 50 s to prepare the nylon printed fabric; the thermal transfer ink is composed of the following weights Percentage of raw material composition: Disperse Yellow 104 Colorant: 32%, Sorbitol: 10%, Butylene Glycol: 10%, Color Fixing Agent: 3%, Defoamer: 0.02%, Surface Tension Regulator: 0.3%, Deionized water: balance.
[0087] Among them, disperse yellow 104 color paste is composed of the following raw materials by weight: disperse yellow 64: 24%, sodium lignosulfonate: 21%, polyester dispersion aid: 18%, deionized water: balance, average particle size The diameter is 100 nm.
[0088] Wherein
Example Embodiment
[0090] Example 3
[0091] A nylon fabric printing production process, comprising the following process steps:
[0092] Step (1) printing the thermal transfer ink on the transfer paper through a digital printing printer;
[0093] Step (2) Transfer the obtained transfer paper to the nylon fabric through a thermal transfer process, and the operating temperature and time are 200 ° C and 45 s, respectively, to prepare a nylon printed fabric; the thermal transfer ink is composed of the following weights Percentage of raw material composition: Disperse Blue 79 Colorant: 35%, Sorbitol: 10%, Butylene Glycol: 10%, Color Fixing Agent: 3.5%, Defoamer: 0.02%, Surface Tension Regulator: 0.2%, Deionized water: balance.
[0094] Among them, disperse blue 79 color paste is composed of the following raw materials by weight: disperse blue 124: 23%, sodium lignosulfonate: 21%, polyether dispersion aid: 16%, γ-butyrolactone: 7%, Deionized water: balance, average particle size is 130 nm.
[0095]
PUM
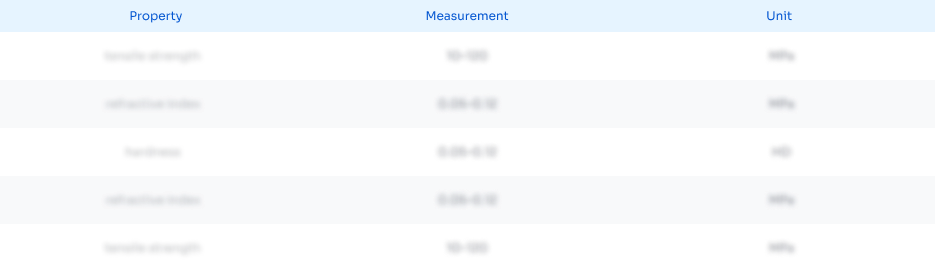
Abstract
Description
Claims
Application Information
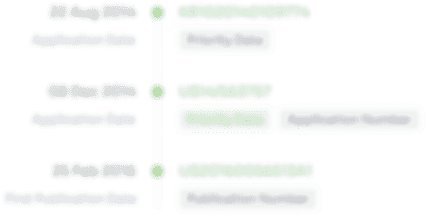
- R&D Engineer
- R&D Manager
- IP Professional
- Industry Leading Data Capabilities
- Powerful AI technology
- Patent DNA Extraction
Browse by: Latest US Patents, China's latest patents, Technical Efficacy Thesaurus, Application Domain, Technology Topic.
© 2024 PatSnap. All rights reserved.Legal|Privacy policy|Modern Slavery Act Transparency Statement|Sitemap