Graphene reinforcing glass fiber for pantograph slide plate and preparation method of graphene reinforcing glass fiber
A pantograph sliding plate and glass fiber technology, which is applied in the field of graphene-reinforced glass fiber for pantograph sliding plates and its preparation, can solve the problems of small elastic modulus of glass fiber, insufficient shear force, non-conductive glass fiber, etc., and achieve High wear resistance, high conductivity, the effect of mature equipment
- Summary
- Abstract
- Description
- Claims
- Application Information
AI Technical Summary
Benefits of technology
Problems solved by technology
Method used
Image
Examples
Embodiment 1
[0028] (1) Glass fiber unbundling: Rinse glass fibers with a radial size of 15-25 μm and a length greater than 1 mm with clean water for 4 times to remove soluble salt and alkali, and disperse the rinsed glass fibers in clean water. Disperse the glass fiber into a single bundle by ultrasonic dispersion, further filter dry, dry, and thermally expand and disperse to obtain unbundled glass fiber;
[0029] (2) Graphene metallization: Mix graphene powder with a radial size of less than 1 μm and a layer thickness of less than 10 nm with copper powder with a particle size of less than 10 μm at a mass ratio of 10:1, and force grinding in a ball mill to make the graphene interface and copper powder Full contact to form graphene-copper powder dispersion;
[0030] (3) Mosaic assembly: mix the unbundled glass fiber obtained in step (1) with the graphene-copper powder dispersion obtained in step (2) metallization at a mass ratio of 100:10, and send it into the air flow disperser, Under the a
Embodiment 2
[0034](1) Glass fiber unbundling: Rinse glass fibers with a radial size of 15-25 μm and a length greater than 1 mm with clean water for 6 times to remove soluble salt and alkali, and disperse the rinsed glass fibers in clean water. Disperse the glass fiber into a single bundle by ultrasonic dispersion, further filter dry, dry, and thermally expand and disperse to obtain unbundled glass fiber;
[0035] (2) Graphene metallization: Mix graphene powder with a radial size of less than 1 μm and a layer thickness of less than 10 nm with aluminum powder with a particle size of less than 10 μm at a mass ratio of 15:1, and force grinding in a ball mill to make the graphene interface and aluminum powder Full contact to form graphene-aluminum powder dispersion;
[0036] (3) Mosaic assembly: mix the unbundled glass fiber obtained in step (1) with the graphene-aluminum powder dispersion obtained in step (2) metallization at a mass ratio of 100:20, and send them into the air flow disperser, Un
Embodiment 3
[0040] (1) Glass fiber unbundling: Rinse glass fibers with a radial size of 15-25 μm and a length greater than 1 mm with clean water for 4 times to remove soluble salt and alkali, and disperse the rinsed glass fibers in clean water. Disperse the glass fiber into a single bundle by ultrasonic dispersion, further filter dry, dry, and thermally expand and disperse to obtain unbundled glass fiber;
[0041] (2) Graphene metallization: Mix graphene powder with a radial size of less than 1 μm and a layer thickness of less than 10 nm with tin powder with a particle size of less than 10 μm at a mass ratio of 20:1, and force grinding in a ball mill to make the graphene interface and tin powder Full contact to form graphene-tin powder dispersion;
[0042] (3) Mosaic assembly: mix the unbundled glass fiber obtained in step (1) with the graphene-tin powder dispersion obtained in step (2) metallization at a mass ratio of 100:25, and send it into the air flow disperser, Under the action of air
PUM
Property | Measurement | Unit |
---|---|---|
Radial size | aaaaa | aaaaa |
Length | aaaaa | aaaaa |
Radial size | aaaaa | aaaaa |
Abstract
Description
Claims
Application Information
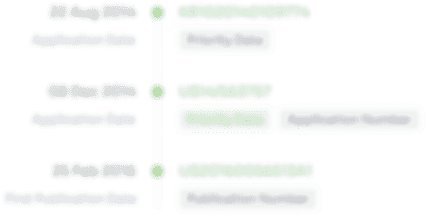
- R&D Engineer
- R&D Manager
- IP Professional
- Industry Leading Data Capabilities
- Powerful AI technology
- Patent DNA Extraction
Browse by: Latest US Patents, China's latest patents, Technical Efficacy Thesaurus, Application Domain, Technology Topic.
© 2024 PatSnap. All rights reserved.Legal|Privacy policy|Modern Slavery Act Transparency Statement|Sitemap