Maintenance method of aluminum alloy hard anodizing electrolyte
A hard anodic oxidation and electrolyte technology, applied in the field of aluminum alloy processing, can solve the problems of wear resistance decline of oxide film, current concentration, burning loss, etc., to improve thickness and hardness, improve heat dissipation effect, and reduce corrosion efficiency. Effect
- Summary
- Abstract
- Description
- Claims
- Application Information
AI Technical Summary
Benefits of technology
Problems solved by technology
Method used
Examples
Embodiment Construction
[0011] Below in conjunction with specific embodiment, further illustrate the present invention, should be understood that these embodiments are only used to illustrate the present invention and are not intended to limit the scope of the present invention, after having read the present invention, those skilled in the art will understand various equivalent forms of the present invention All modifications fall within the scope defined by the appended claims of the present application.
[0012] The hard anodic oxidation process of the present invention is mainly used to prepare a layer of wear-resistant oxide layer on the surface of the rotating platen of the air-conditioning compressor, so as to improve the running wear resistance and service life. After the aluminum alloy parts of the rotary platen are machined and formed, they are degreased, washed with water, alkali-etched, washed with water, light-extracted and washed with water in sequence, and then anodized.
[0013] Electroly
PUM
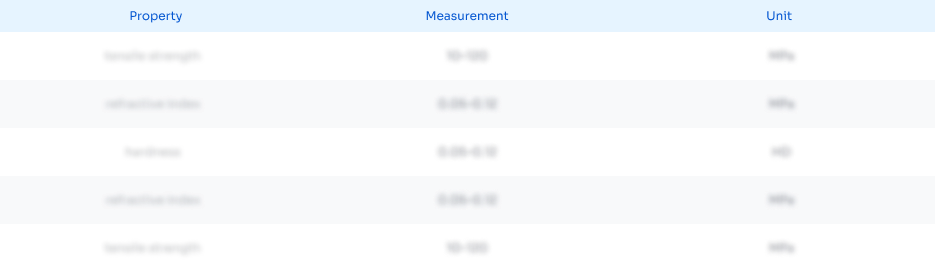
Abstract
Description
Claims
Application Information
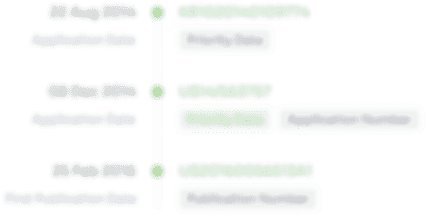
- R&D Engineer
- R&D Manager
- IP Professional
- Industry Leading Data Capabilities
- Powerful AI technology
- Patent DNA Extraction
Browse by: Latest US Patents, China's latest patents, Technical Efficacy Thesaurus, Application Domain, Technology Topic.
© 2024 PatSnap. All rights reserved.Legal|Privacy policy|Modern Slavery Act Transparency Statement|Sitemap