Method for extracting iron from high-iron low-silicon type laterite ore
A technology of laterite and iron ore, which is applied in the direction of improving process efficiency, etc., to achieve low alkali consumption, high-efficiency separation, and increase the utilization coefficient of blast furnaces
- Summary
- Abstract
- Description
- Claims
- Application Information
AI Technical Summary
Problems solved by technology
Method used
Image
Examples
Embodiment 1
[0023] Such as figure 1 shown.
[0024] The mass content of Fe is 40.1%, SiO 2 The content is 2.98%, Al 2 o 3 The laterite iron ore with a content of 11.96% is placed in a NaOH alkali solution with a mass concentration of 55%, and is subjected to alkali leaching reaction in a closed container at a temperature of 120°C for 6.0 hours, and then the reactant is filtered to obtain an alkali leaching filter cake A and filtrate B, NaOH consumption 14.0 kg / t feed ore, its chemical reaction formula is:
[0025] Al 2 o 3 +2NaOH 2NaAlO 2 + H 2 o
[0026] tSiO 2 +2NaOH Na 2 O (SiO 2 ) t ↓ + H 2 o
[0027] Filter cake A is the final iron ore concentrate obtained with a TFe content of 66.8%, in which SiO2 The content is 0.45%, Al 2 o 3 The S content is 0.96%, and the S content is 0.02%; the filtrate B is fed into the recycling system.
Embodiment 2
[0029] The TFe content is 49.8%, SiO 2 The content is 0.22%, Al 2 o 3 The laterite iron ore with a content of 8.10% is placed in a NaOH alkali solution with a mass concentration of 4%, and is subjected to alkali leaching reaction in a closed container at a temperature of 210°C for 0.3 hours, and then the reactant is filtered to obtain an alkali leaching filter cake A and filtrate B, NaOH consumption 10.36kg / t feed ore, its chemical reaction formula is the same as embodiment 1.
[0030] Filter cake A is the final iron ore concentrate obtained with a TFe content of 62.1%, in which SiO 2 The content is 0.08%, Al 2 o 3 The content of S is 0.87%, and the content of S is 0.01%; the filtrate B is fed into the recycling system.
Embodiment 3
[0032] The TFe content is 44.2%, SiO 2 The content is 2.54%, Al 2 o 3 The laterite iron ore with a content of 10.82% is placed in a NaOH alkali solution with a mass concentration of 50%, and the alkali leaching reaction is carried out in a closed container at a temperature of 200°C for 4.0 hours, and then the reactant is filtered to obtain an alkali leaching filter cake A and filtrate B, NaOH consumption 19.89kg / t feed ore, its chemical reaction formula is the same as embodiment 1.
[0033] Filter cake A is the final iron ore concentrate obtained with a TFe content of 67.90%, in which SiO 2 The content is 0.12%, Al 2 o 3 The content is 0.66%, and the S content is 0.01%; the filtrate B is fed into the recycling system.
PUM
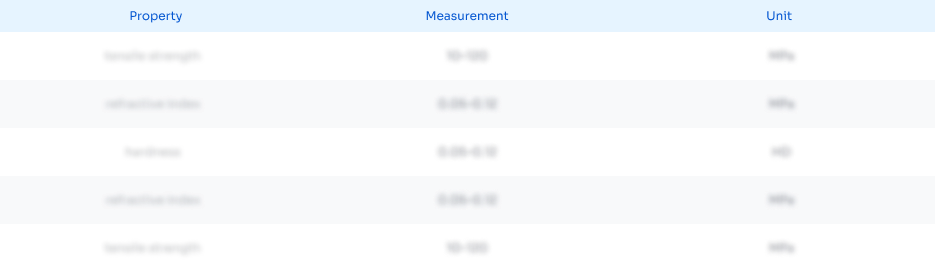
Abstract
Description
Claims
Application Information
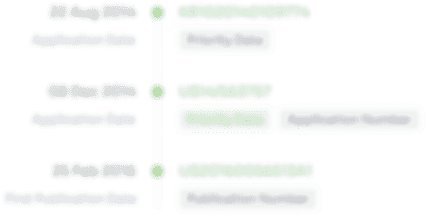
- R&D Engineer
- R&D Manager
- IP Professional
- Industry Leading Data Capabilities
- Powerful AI technology
- Patent DNA Extraction
Browse by: Latest US Patents, China's latest patents, Technical Efficacy Thesaurus, Application Domain, Technology Topic.
© 2024 PatSnap. All rights reserved.Legal|Privacy policy|Modern Slavery Act Transparency Statement|Sitemap