Organosilicon composition and preparation method thereof
A composition and silicone technology, applied in the field of silicone, can solve problems such as strong adhesion, unsatisfactory use effect, and insufficient strength, and achieve the effect of high fluidity and good storage stability
- Summary
- Abstract
- Description
- Claims
- Application Information
AI Technical Summary
Problems solved by technology
Method used
Examples
Example
[0027] Preparation Example 1
[0028] The preparation process of the organosilicon composition of the present invention includes the following steps:
[0029] S1. Preparation of the base material: 150g of α,ω-dihydroxypolydimethylsiloxane with 20000 cPs, 75g of α,ω-dihydroxypolydimethylsiloxane with 50000 cPs, and end-capped α,ω- with 33000cPs Dihydroxy dimethicone 225g, 500cPs α,ω-dihydroxy dimethicone 10g and white carbon black 26.8g mixed well, then add 12g black paste, continue to mix until uniform, then put it into the planetary machine Evacuate air bubbles for 60 minutes, vacuumize for 15 minutes, add 300 g of volatile silicone oil and stir for 30 minutes after maintaining pressure;
[0030] S2. Preparation of the organosilicon composition: adding the matrix material prepared in S1 to 2% trimethoxysilane by weight of the matrix material prepared in S1 and 1% by weight of the matrix material prepared in S1. Butyl ester, mixed evenly under the isolation of air, ready to be obtain
Example
[0031] Preparation Example 2
[0032] The preparation process of the organosilicon composition of the present invention includes the following steps:
[0033] S1. Preparation of the base material: 150g of α,ω-dihydroxypolydimethylsiloxane with 20000 cPs, 75g of α,ω-dihydroxypolydimethylsiloxane with 50000 cPs, and end-capped α,ω- with 33000cPs Dihydroxy dimethicone 225g, 500cPs α,ω-dihydroxy dimethicone 10g and white carbon black 214.4g are mixed uniformly, then add 12g black paste, continue to mix until uniform, then put it into the planetary machine Evacuate air bubbles for 60 minutes, vacuum for 15 minutes, add 600g of volatile silicone oil, and stir for 30 minutes after maintaining pressure;
[0034] S2. Preparation of the organosilicon composition: adding the matrix material prepared in S1 to 8% trimethoxysilane by weight of the matrix material prepared in S1 and 3% by weight of the matrix material prepared in S1 tetrabutyl titanate , Mix uniformly under isolation of air, and ge
Example
[0035] Preparation Example 3
[0036] The preparation process of the organosilicon composition of the present invention includes the following steps:
[0037] S1. Preparation of the base material: 150g of α,ω-dihydroxypolydimethylsiloxane with 20000 cPs, 75g of α,ω-dihydroxypolydimethylsiloxane with 50000 cPs, and end-capped α,ω- with 33000cPs Dihydroxy polydimethylsiloxane 225g, 500cPs α,ω-dihydroxy polydimethylsiloxane 10g and white carbon black 110g are mixed uniformly, then add 12g black paste, continue to mix until uniform, and then put it into the planetary machine Evacuate air bubbles for 60 minutes, vacuum for 15 minutes, add 600g of volatile silicone oil and stir for 30 minutes after maintaining pressure;
[0038] S2. Preparation of the organosilicon composition: adding the base material prepared in S1 to 4.46% trimethoxysilane by weight of the base material prepared in S1 and 3% tetrabutyl titanate by weight of the base material prepared in S1 , Mix uniformly under isolatio
PUM
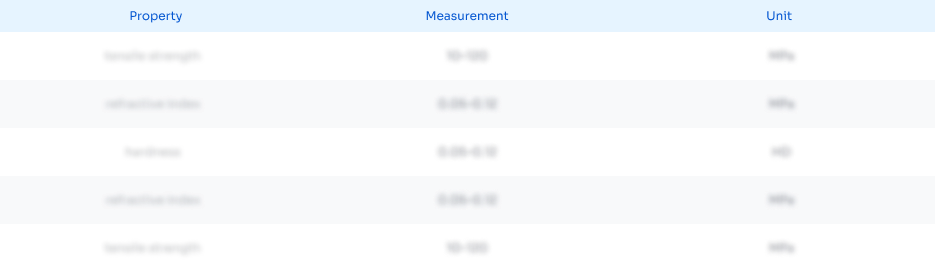
Abstract
Description
Claims
Application Information
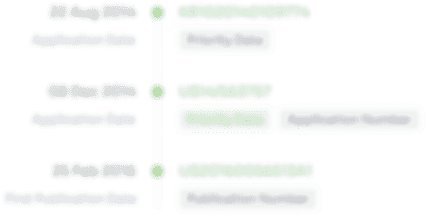
- R&D Engineer
- R&D Manager
- IP Professional
- Industry Leading Data Capabilities
- Powerful AI technology
- Patent DNA Extraction
Browse by: Latest US Patents, China's latest patents, Technical Efficacy Thesaurus, Application Domain, Technology Topic.
© 2024 PatSnap. All rights reserved.Legal|Privacy policy|Modern Slavery Act Transparency Statement|Sitemap