Electrolytic manganese residue-red mud cement and preparation method thereof
A technology of electrolytic manganese slag and red mud, applied in cement production, etc., can solve problems such as frosting, achieve low total ammonia content, high compressive strength and flexural strength, and reduce the effect of cement blooming
- Summary
- Abstract
- Description
- Claims
- Application Information
AI Technical Summary
Problems solved by technology
Method used
Examples
Example Embodiment
[0015] The preparation method of electrolytic manganese slag-red mud cement of the present invention may include material preparation, first calcination, preparation of slurry, baking, second calcination, and third calcination.
[0016] In detail, the above-mentioned materials may include 30-60 parts by weight of manganese slag, 10-20 parts by weight of red mud, 3-5 parts by weight of slag powder, 3-8 parts by weight of alkaline modifier, 3-5 parts by weight of cement raw meal, 25-30 parts by weight of cement clinker and 1-3 parts by weight of water reducing agent.
[0017] The above-mentioned first calcination may include mixing manganese slag and slag powder, and calcination at a temperature of 400-500° C. to obtain the first calcination product. Preferably, the first calcination time can be 1-2h, and the particle size of manganese slag and slag powder can be 200-300 mesh.
[0018] The first calcined product and red mud obtained after the first calcining are added to water, and then
Example Embodiment
[0025] Example 1
[0026] Preparation: 30 parts by weight of manganese slag, 10 parts by weight of red mud, 5 parts by weight of slag powder, 3 parts by weight of alkaline modifier, 5 parts by weight of cement raw meal, 25 parts by weight of cement clinker and 1 Parts by weight of water reducing agent; among them, the alkaline modifier is CaO, and the water reducing agent is NaSiO 4 .
[0027] After mixing manganese slag (300 mesh) and slag powder (200 mesh), they are calcined at a temperature of 400° C. for 2 hours to obtain the first calcined product.
[0028] Add the first calcined product and red mud to water at a temperature of 90°C and stir at a stirring speed of 1000r / min. After stirring for 5 minutes, add an alkaline modifier and continue stirring. The total stirring time is 30min, and keep the temperature of the mixture at 90°C during the stirring process to obtain a slurry.
[0029] After the slurry is allowed to stand and settle, the water in the upper layer is removed, and
Example Embodiment
[0032] Example 2
[0033] Material preparation: 60 parts by weight of manganese slag, 20 parts by weight of red mud, 3 parts by weight of slag powder, 8 parts by weight of alkaline modifier, 3 parts by weight of cement raw meal, 30 parts by weight of cement clinker and 3 parts by weight Parts by weight of water reducing agent; among them, the alkaline modifier is MgO and the water reducing agent is NaSiO 4 And a mixture of sodium carboxylate.
[0034] After mixing manganese slag (200 mesh) and slag powder (300 mesh), they are calcined at a temperature of 500° C. for 1 h to obtain the first calcined product.
[0035] Add the first calcined product and red mud to water at a temperature of 120°C and stir at a stirring speed of 500r / min. After stirring for 10 minutes, add an alkaline modifier and continue stirring. The total stirring time is 60min, and keep the temperature of the mixture at 110°C during the stirring process to obtain a slurry.
[0036] After the slurry is allowed to stand
PUM
Property | Measurement | Unit |
---|---|---|
Particle size | aaaaa | aaaaa |
Abstract
Description
Claims
Application Information
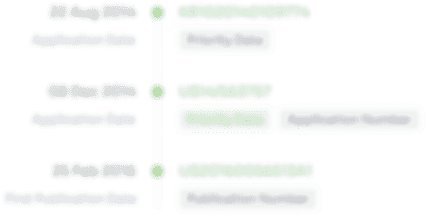
- R&D Engineer
- R&D Manager
- IP Professional
- Industry Leading Data Capabilities
- Powerful AI technology
- Patent DNA Extraction
Browse by: Latest US Patents, China's latest patents, Technical Efficacy Thesaurus, Application Domain, Technology Topic.
© 2024 PatSnap. All rights reserved.Legal|Privacy policy|Modern Slavery Act Transparency Statement|Sitemap