Refractory wear-resistant pouring material and preparation method thereof
A fire-resistant, wear-resistant, castable technology, applied in the field of coagulation pouring, can solve problems such as poor stability, poor fluidity, difficulty in mass pouring, and low demoulding strength, so as to improve fluidity, improve mechanical strength, and reduce pretreatment The effect of the process
- Summary
- Abstract
- Description
- Claims
- Application Information
AI Technical Summary
Problems solved by technology
Method used
Examples
Example Embodiment
[0044] The specific steps of the preparation method of refractory and wear-resistant castable are as follows:
[0045] Step 1. Preparation of composite glue
[0046] Take appropriate mass ratio of polyvinyl alcohol, water-soluble nano-grade silica sol, kaolin, vinyl triethoxysilane, boron fiber powder, and retarder to mix uniformly to prepare a composite glue;
[0047] Step two, prepare mixed matrix slurry
[0048] Take the ground natural river sand, micro-alumina powder, micro-silica powder, micro-steel fiber, and dispersant solution of appropriate mass ratio and particle size, and mix them uniformly to form a slurry that has the fluidity that can be poured in a mold;
[0049] Step three, prepare refractory and wear-resistant castable
[0050] Add the composite glue prepared in step 1 of the appropriate mass ratio to the graded ceramic particles with the appropriate mass ratio. The composite glue forms a gel around the particles, and then vacuum filtration and drying are performed. The gel
Example Embodiment
[0051] Implementation case 1
[0052] Step 1. Preparation of composite glue
[0053] Take appropriate mass ratio of polyvinyl alcohol (35%), water-soluble nano-scale silica sol (44.8%), kaolin (12%), vinyl triethoxysilane (0.2%), boron fiber powder (8%), Retarder (organic acid retarder 0.001%) is mixed uniformly to prepare composite glue;
[0054] Step two, prepare mixed matrix slurry
[0055] Take the ground natural river sand (15%, 5μm), alumina powder (10%, 5μm), microsilica powder (15%, 1μm), micro steel fiber (15%, 0.1mm) and Dispersant solution (45%, 15% sodium citrate solution), mixed uniformly to form a slurry, with fluidity that can be poured in a mold;
[0056] Step three, prepare refractory and wear-resistant castable
[0057] Step 1 of adding proper mass ratio to the graded ceramic particles (8~5mm: 5~3mm: 3~1mm: 1~0mm=35%: 25%: 35%: 5%) with mass ratio (65%) The prepared composite glue (15%), the composite glue forms a gel around the particles, then vacuum filtration and dry
Example Embodiment
[0058] Implementation case 2
[0059] Step 1. Preparation of composite glue
[0060] Take appropriate mass ratio of polyvinyl alcohol (20%), water-soluble nano-scale silica sol (55%), kaolin (20%), vinyl triethoxy silane (0.8%), boron fiber powder (4.2%), Retarder (organic acid retarder 0.001%) is mixed uniformly to prepare composite glue;
[0061] Step two, prepare mixed matrix slurry
[0062] Take the ground natural river sand (20%, 10μm), alumina powder (12%, 8μm), microsilica powder (20%, 1μm), micro steel fiber (18%, 0.1mm) and Dispersant solution (40%, 15% sodium citrate solution), mixed uniformly to form a slurry, with fluidity that can be poured in a mold;
[0063] Step three, prepare refractory and wear-resistant castable
[0064] Step 1 of adding an appropriate mass ratio to the graded ceramic particles (8~5mm: 5~3mm: 3~1mm: 1~0mm=40%:30%:20%:10%) with a mass ratio (60%) The prepared composite glue (12%), the composite glue forms a gel around the particles, then vacuum filtrati
PUM
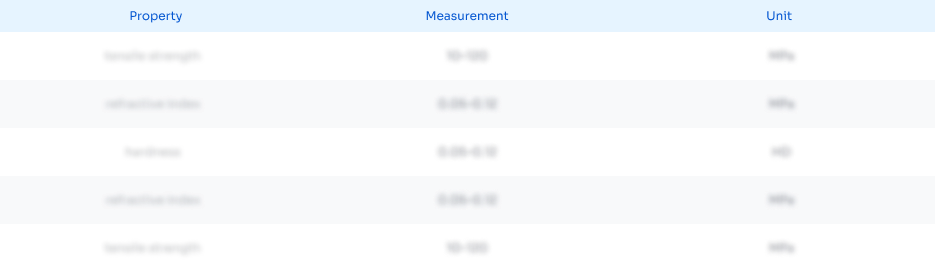
Abstract
Description
Claims
Application Information
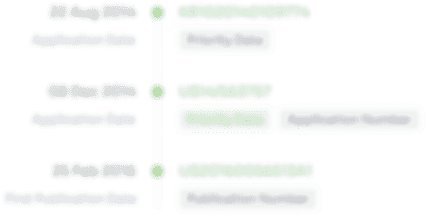
- R&D Engineer
- R&D Manager
- IP Professional
- Industry Leading Data Capabilities
- Powerful AI technology
- Patent DNA Extraction
Browse by: Latest US Patents, China's latest patents, Technical Efficacy Thesaurus, Application Domain, Technology Topic.
© 2024 PatSnap. All rights reserved.Legal|Privacy policy|Modern Slavery Act Transparency Statement|Sitemap