Hydrogen-rich oxygen blast furnace ironmaking method
An oxygen and blast furnace technology, which is applied in the field of circulating gas upgrading and using hydrogen-rich oxygen blast furnace ironmaking, can solve the problems of reduced gas volume, insufficient preheating of furnace materials, energy loss, etc., and achieves reduction and optimization of coke consumption. effect, the effect of reducing inaccuracy
- Summary
- Abstract
- Description
- Claims
- Application Information
AI Technical Summary
Benefits of technology
Problems solved by technology
Method used
Image
Examples
Embodiment 1
[0024] Such as figure 1 As shown, a method for ironmaking of a hydrogen-oxygen-rich blast furnace includes the following steps and device setting method:
[0025] (1) Pure oxygen, pulverized coal, hydrogen and high-temperature upgrading gas are introduced into the middle and lower part of the hearth of the oxygen blast furnace, and high-temperature upgrading gas is also introduced into the lower part of the furnace shaft of the oxygen blast furnace, and ore and coke are added to the top of the oxygen blast furnace , the top gas generated at the top of the furnace is passed into the gas upgrading heating furnace through the pipeline, and high-temperature upgrading gas and low-temperature upgrading gas are formed in the gas upgrading heating furnace, wherein the high-temperature upgrading gas passes through the lower part of the furnace body and the hearth The middle and lower parts are passed into the oxygen blast furnace again.
[0026] The temperature at which the high-temperat
Embodiment 2
[0035] Such as figure 1 Shown: a hydrogen-oxygen-rich blast furnace ironmaking method, including the following steps and device settings:
[0036] (1) Pure oxygen, pulverized coal, hydrogen and high-temperature upgrading gas are introduced into the middle and lower part of the hearth of the oxygen blast furnace, and high-temperature upgrading gas is also introduced into the lower part of the furnace shaft of the oxygen blast furnace, and ore and coke are added to the top of the oxygen blast furnace , the top gas generated at the top of the furnace is passed into the gas upgrading heating furnace through the pipeline, and high-temperature upgrading gas and low-temperature upgrading gas are formed in the gas upgrading heating furnace, wherein the high-temperature upgrading gas passes through the lower part of the furnace body and the hearth The middle and lower parts are passed into the oxygen blast furnace again.
[0037] (2) The oxygen blast furnace is provided with an oxygen bl
Embodiment 3
[0047] The setting method of the hydrogen-oxygen rich blast furnace device:
[0048] Such as figure 1 shown.
[0049] The oxygen blast furnace is provided with an oxygen blast port, a coal injection port, a hydrogen inlet and a lower upgraded gas inlet in the lower part of the furnace hearth, and an upper upgraded gas inlet is arranged at the lower part of the blast furnace body. The oxygen blast port is used for blowing into pure oxygen, the coal injection port is used to inject coal powder, the hydrogen inlet is used to inject hydrogen, the lower upgraded gas inlet and the upper upgraded gas inlet are used to blast high-temperature upgraded gas generated from the gas upgrading heating furnace .
[0050] The gas upgrading heating furnace includes an upper inner pipe, a lower outer pipe, a reaction chamber, a liquid slag chamber and a pulverized coal feeding device. The upper inner pipe is inserted into the lower outer pipe, and the upper inner pipe and the lower outer pipe are
PUM
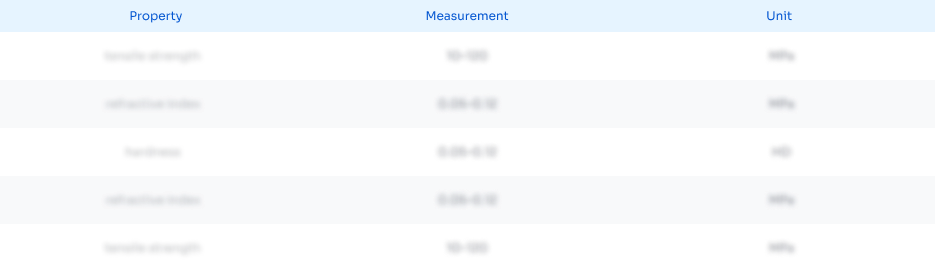
Abstract
Description
Claims
Application Information
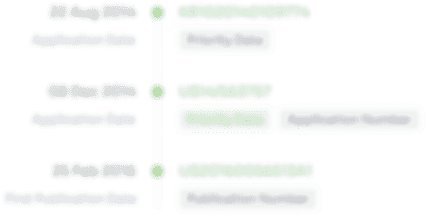
- R&D Engineer
- R&D Manager
- IP Professional
- Industry Leading Data Capabilities
- Powerful AI technology
- Patent DNA Extraction
Browse by: Latest US Patents, China's latest patents, Technical Efficacy Thesaurus, Application Domain, Technology Topic.
© 2024 PatSnap. All rights reserved.Legal|Privacy policy|Modern Slavery Act Transparency Statement|Sitemap