Laser welding method of CoCrCuFeNi high-entropy alloy
A technology of laser welding and high-entropy alloys, applied in laser welding equipment, welding equipment, metal processing equipment, etc., can solve problems such as cold cracks, hot cracks, alloy welding difficulties, etc., and achieve high strength and plasticity
- Summary
- Abstract
- Description
- Claims
- Application Information
AI Technical Summary
Benefits of technology
Problems solved by technology
Method used
Image
Examples
Embodiment 1
[0024] Two pieces of CoCrCuFeNi high-entropy alloy with dimensions of 200 × 50 × 3 mm were welded.
[0025] Welding process: Open a V-shaped groove, use acetone to ultrasonically clean it for 30 minutes, apply TiO metal paste 30 μm on the surface of the groove, and dry it naturally for 24 hours before performing laser cladding; the laser cladding power is set to 700W, and the scanning speed is 0.5m / min, circular spot, the diameter of the spot is 1.5mm, the protective gas is argon, and the gas flow rate is set to 10L / min; after cladding, apply TiO metal paste for the second time, with a thickness of 50μm, and dry naturally After 24 hours, laser welding is carried out; the laser power is set to 1200W, the welding speed is set to 0.1m / min, the spot is a circular spot with a diameter of 3mm, the laser cladding protective gas is argon, and the gas flow rate is 13L / min .
[0026] TiO metal paste composition: TiO powder 3g, titanium powder 1g, aluminum powder 1g, diethyl oxalat
Embodiment 2
[0029] Welding of two CoCrCuFeNi high-entropy alloys with dimensions of 400×10×3 and 200×10×3 mm;
[0030] Welding process: open a V-shaped groove, use acetone to ultrasonically clean it for 30 minutes, apply TiO metal paste 50 μm on the surface of the groove, and dry it naturally for 24 hours before performing laser cladding; the laser cladding power is set to 1000W, and the scanning speed is 0.3m / min, circular spot, the diameter of the spot is 2mm, the protective gas is argon, and the gas flow rate is set to 15L / min; after cladding, apply TiO metal paste for the second time, with a thickness of 40μm, and dry it naturally for 24 Hours later, laser welding was performed; the laser power was set to 1200W, the welding speed was set to 0.1m / min, the spot was a circular spot with a diameter of 3mm, the laser cladding protective gas was argon, and the gas flow rate was 13L / min.
[0031] TiO metal slurry composition: TiO powder 5g, titanium powder 0.6g, aluminum powder 0.7g, di
Embodiment 3
[0033] Welding of two CoCrCuFeNi high-entropy alloys with dimensions of 800×100×3 and 20×100×3 mm;
[0034] Welding process: Open a V-shaped groove, use acetone to ultrasonically clean it for 30 minutes, apply TiO metal paste 10 μm on the surface of the groove, and dry it naturally for 24 hours before performing laser cladding; the laser cladding power is set to 2500W, and the scanning speed is 0.4m / min, circular spot, the diameter of the spot is 1.5mm, the protective gas is argon, and the gas flow rate is set to 25L / min; after cladding, apply TiO metal paste for the second time, with a thickness of 80μm, and dry naturally After 24 hours, laser welding is carried out; the laser power is set to 1200W, the welding speed is set to 0.1m / min, the spot is a circular spot with a diameter of 3mm, the laser cladding protective gas is argon, and the gas flow rate is 13L / min .
[0035] TiO metal paste composition: TiO powder 2.5g, titanium powder 0.9g, aluminum powder 0.9g, diethyl
PUM
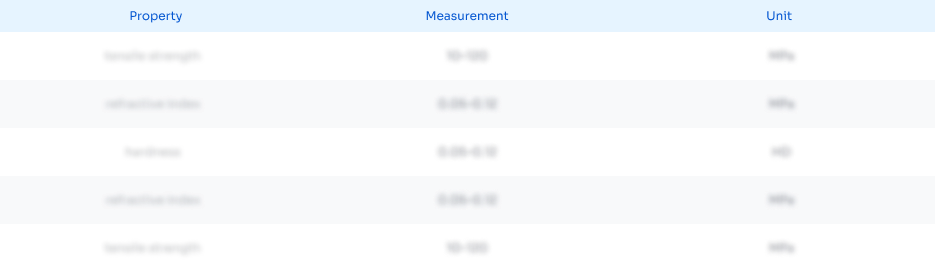
Abstract
Description
Claims
Application Information
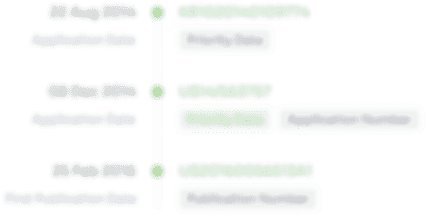
- R&D Engineer
- R&D Manager
- IP Professional
- Industry Leading Data Capabilities
- Powerful AI technology
- Patent DNA Extraction
Browse by: Latest US Patents, China's latest patents, Technical Efficacy Thesaurus, Application Domain, Technology Topic.
© 2024 PatSnap. All rights reserved.Legal|Privacy policy|Modern Slavery Act Transparency Statement|Sitemap