Identical pulp transfer printing method of cotton-polyester blended fabric
A cotton-polyester blending and transfer printing technology, which is applied in the field of textile printing, can solve the problems of poor sun resistance and waterproof performance, not full and unbright colors, and limited development and application, and achieves good sun exposure and waterproof performance. Bright, water-saving effect
- Summary
- Abstract
- Description
- Claims
- Application Information
AI Technical Summary
Problems solved by technology
Method used
Examples
Embodiment 1
[0034] Use polyester-cotton blended (T / C=65:35) woven bleached cloth
[0035] Follow these steps:
[0036] (1) Configure printing paste: 1% to 20% of polymer starch, 0.01% to 2% of surfactant, 0.02% to 2% of leveling agent, 15% of reactive dye, 15% of disperse dye and the rest of water. Grinding in a ball mill for 8-12 hours, the high molecular weight starch is non-ionic or cationic or anionic.
[0037] (2) Printing: Print the printing paste on the PET film with a gravure printing machine; place the cotton-polyester blended fabric on an aluminum plate or a plastic plate, with a padding pressure of 15 tons, and dip into 40g / l color-fixing liquid; the blended fabric The fabric and the PET film are closely attached, and the pattern on the PET film is transferred to the blended fabric under high pressure. The transfer pressure is 50 tons and the speed is 25 m / min.
[0038] (3) Color fixation: Dry the cotton-polyester blended fabric fabric after pattern transfer, and then stea
Embodiment 2
[0041] Use polyester-cotton blended (T / C=50:50) woven bleached cloth
[0042] Follow these steps:
[0043] (1) Configure printing paste: 1% to 20% of polymer starch, 0.01% to 2% of surfactant, 0.02% to 2% of leveling agent, 15% of reactive dye, 15% of disperse dye and the rest of water. Grinding in a ball mill for 8-12 hours, the high molecular weight starch is non-ionic or cationic or anionic.
[0044](2) Printing: use a gravure printing machine to print the printing paste on the transfer paper; place the cotton-polyester blended fabric on an aluminum plate or a plastic plate, with a padding pressure of 20 tons, and dip into 40g / l color-fixing liquid; The polyester blended fabric and the transfer paper are closely bonded. Under high pressure, the pattern on the transfer paper is transferred to the cotton polyester blended fabric. The transfer pressure is 40 tons and the speed is 30 m / min.
[0045] (3) Color fixation: Dry the cotton-polyester blended fabric fabric after p
PUM
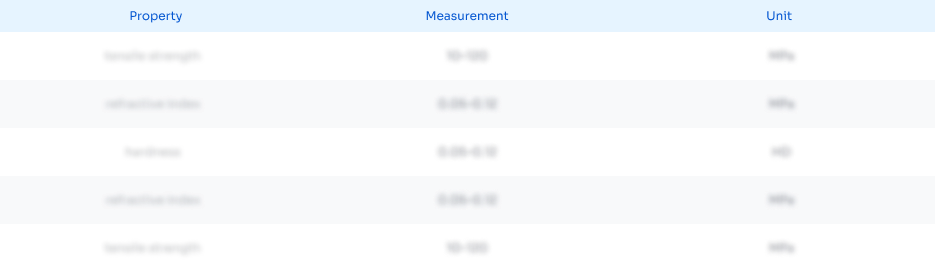
Abstract
Description
Claims
Application Information
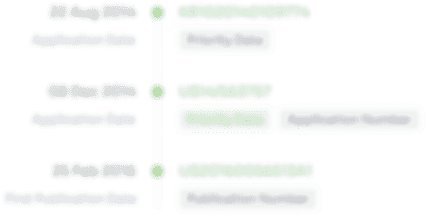
- R&D Engineer
- R&D Manager
- IP Professional
- Industry Leading Data Capabilities
- Powerful AI technology
- Patent DNA Extraction
Browse by: Latest US Patents, China's latest patents, Technical Efficacy Thesaurus, Application Domain, Technology Topic.
© 2024 PatSnap. All rights reserved.Legal|Privacy policy|Modern Slavery Act Transparency Statement|Sitemap