Method for improving performance of superplastic formed component material
A technology of superplastic forming and material properties, applied in the field of superplastic forming, can solve the problems of weak second phase, high difficulty and high cost, and achieve the effect of reducing size and area, improving component performance and low cost
- Summary
- Abstract
- Description
- Claims
- Application Information
AI Technical Summary
Benefits of technology
Problems solved by technology
Method used
Image
Examples
Embodiment Construction
[0029] The invention provides a method for improving the material properties of superplastic forming components. By applying a short-time pulse current to superplastic forming components such as aluminum alloy, aluminum-lithium alloy, and magnesium alloy, internal voids are reduced and component performance is improved. The present invention will be further described in detail through the accompanying drawings and specific embodiments below.
[0030] As shown in the figure, this embodiment takes high-temperature superplastic inflation forming of a 7B04 aluminum alloy cylindrical part as an example by applying a pulse current, and the specific implementation steps are as follows:
[0031] 1. Current loop design.
[0032] According to the characteristics of the cylindrical part, the current circuit design is carried out, and the follow-up electrodes 4 and 5 attached to the cylindrical part are installed in the lower mold 2 of the forming mold. In this embodiment, the follow-up elec
PUM
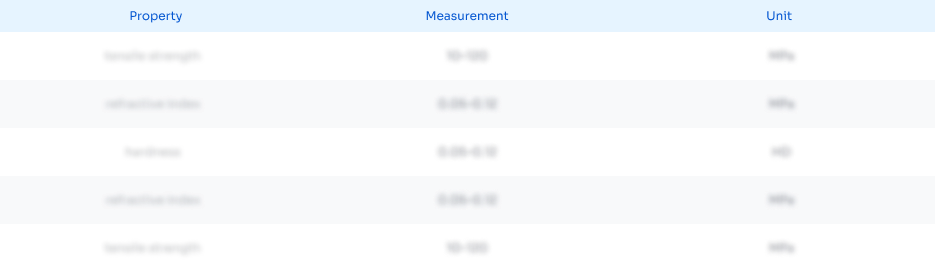
Abstract
Description
Claims
Application Information
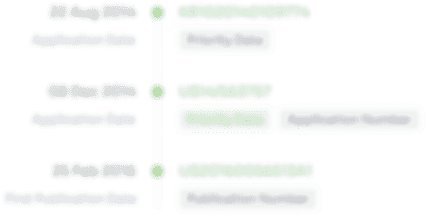
- R&D Engineer
- R&D Manager
- IP Professional
- Industry Leading Data Capabilities
- Powerful AI technology
- Patent DNA Extraction
Browse by: Latest US Patents, China's latest patents, Technical Efficacy Thesaurus, Application Domain, Technology Topic.
© 2024 PatSnap. All rights reserved.Legal|Privacy policy|Modern Slavery Act Transparency Statement|Sitemap