Liquid cement grinding aid and preparation method thereof
The invention relates to a technology of a cement grinding aid and a manufacturing method, which is applied in the field of concrete admixture preparation, and can solve the problems of unstable quality and large dosage of the grinding aid, and achieve the effects of increased strength, low dosage and increased specific surface area.
- Summary
- Abstract
- Description
- Claims
- Application Information
AI Technical Summary
Benefits of technology
Problems solved by technology
Method used
Image
Examples
Embodiment 1
[0024] A liquid cement grinding aid and a manufacturing method thereof, comprising the following components, by mass percentage:
[0025] High molecular polymer: 50%
[0026] Sulfuran: 5%
[0027] Propylene Glycol: 11%
[0028] Ammonium nitrate: 5%
[0029] Water: 40%
[0030] The preparation process of this cement grinding aid is as follows:
[0031] In the state of stirring, add p-aminobenzenesulfonic acid, propylene glycol, and ammonium nitrate to the water in sequence, and then add the high-molecular polymer until it is completely dissolved, and stir until the high-molecular polymer is completely dissolved. The preparation method is as follows, in terms of mass percentage:
[0032] Take 71.2% acetone in a four-necked flask, then add 0.5% azobisisobutyronitrile and 0.3% n-dodecanethiol respectively, start stirring, heat up to 60°C and reflux, add 2% styrene, 20 % allyl ether (n=25), 6% ethyl acrylate monomer; control the temperature at 60±1° C., and react for 3.5 hours.
Embodiment 2
[0034] A liquid cement grinding aid and a manufacturing method thereof, comprising the following components, by mass percentage:
[0035] High molecular polymer: 50%
[0036] Sulfuran: 3%
[0037] Propylene Glycol: 10%
[0038] Ammonium nitrate: 4%
[0039] Water: 33%
[0040] The preparation process of this cement grinding aid is as follows:
[0041] While stirring, add p-sulfanilic acid, propylene glycol, and ammonium nitrate to the water in sequence until they are completely dissolved, then add the high molecular polymer, and stir until they are completely dissolved.
[0042] The preparation method of macromolecular polymer is as follows, by mass percentage:
[0043] Take 69.1% acetone in a four-necked flask, then add 0.6% azobisisobutyronitrile and 0.3% n-dodecanethiol respectively, start stirring, raise the temperature to 58°C and reflux, add 2% styrene, 22% Allyl ether (n=28), 6% ethyl acrylate monomer; control temperature at 59±1°C, react for 4 hours. After the reac
Embodiment 3
[0045] A liquid cement grinding aid and a manufacturing method thereof, comprising the following components, by mass percentage:
[0046] High molecular polymer: 60%
[0047] Sulfuran: 5%
[0048] Propylene Glycol: 5%
[0049] Ammonium nitrate: 1%
[0050] Water: 29%
[0051] The preparation process of this cement grinding aid is as follows:
[0052] While stirring, add p-sulfanilic acid, propylene glycol, and ammonium nitrate to the water in sequence until they are completely dissolved, then add the high molecular polymer, and stir until they are completely dissolved.
[0053] The preparation method of macromolecular polymer is as follows, by mass percentage:
[0054] Take 69% acetone in a four-necked flask, then add 0.8% azobisisobutyronitrile and 0.2% n-dodecanethiol respectively, start stirring, raise the temperature to 58°C and reflux, add 2.2% styrene, 23.8% Allyl ether (n=28), 4% ethyl acrylate monomer; control temperature at 58±1° C., react for 5 hours. After the r
PUM
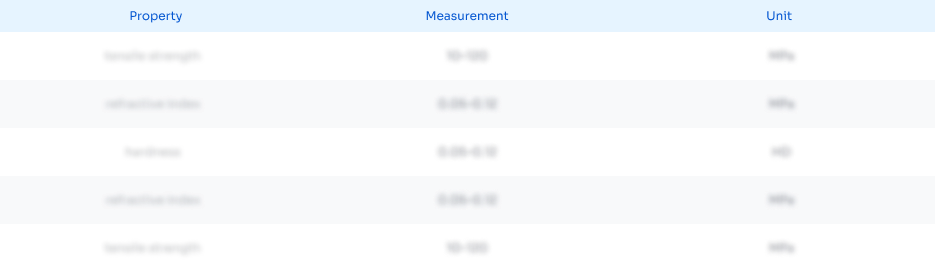
Abstract
Description
Claims
Application Information
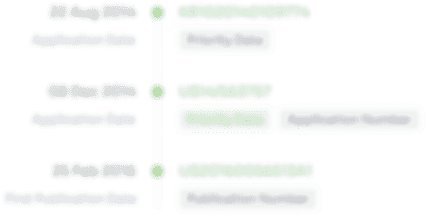
- R&D Engineer
- R&D Manager
- IP Professional
- Industry Leading Data Capabilities
- Powerful AI technology
- Patent DNA Extraction
Browse by: Latest US Patents, China's latest patents, Technical Efficacy Thesaurus, Application Domain, Technology Topic.
© 2024 PatSnap. All rights reserved.Legal|Privacy policy|Modern Slavery Act Transparency Statement|Sitemap