Sheath-core flame retardant filament and preparation method thereof
A skin-core and filament technology, applied in the field of fibers, can solve the problems of poor flame retardancy and slow natural degradation rate of polyester-nylon composite filaments, and achieve the effects of enhancing offensive ability, improving degradation rate and increasing specific surface area.
- Summary
- Abstract
- Description
- Claims
- Application Information
AI Technical Summary
Problems solved by technology
Method used
Examples
Embodiment 1
[0042] A preparation method of a skin-core flame-retardant filament, the steps of which are as follows:
[0043] (1) prepare MgO powder;
[0044] First heat MgO to 400°C and keep it warm for 2 hours, then raise the temperature to 700°C and keep it warm for 1 hour, then cool it in the air, and finally pulverize it to obtain MgO powder with an average particle size of 0.49 microns;
[0045] (2) prepare polyester;
[0046] (2.1) Esterification reaction;
[0047] Make slurry with terephthalic acid, ethylene glycol and 2-carboxyethylphenylphosphinic acid at a molar ratio of 1:1.2:0.03, add MgO powder, antimony trioxide, titanium dioxide and trimethyl phosphate and mix well Finally, the esterification reaction is carried out under pressure in a nitrogen atmosphere. The pressurized pressure is 0.3 MPa, and the temperature of the esterification reaction is 250 ° C. When the amount of water distilled in the esterification reaction reaches 90.1% of the theoretical value, it is an esterif
Embodiment 2
[0056] A preparation method of a skin-core flame-retardant filament, the steps of which are as follows:
[0057] (1) prepare BaO powder;
[0058] First heat BaO to 400°C and keep it warm for 3 hours, then raise the temperature to 700°C and keep it warm for 2 hours, then cool it in the air, and finally pulverize it to obtain BaO powder with an average particle size of 0.45 microns;
[0059] (2) prepare polyester;
[0060] (2.1) Esterification reaction;
[0061] Make slurry with terephthalic acid, ethylene glycol and 2-carboxyethylphenylphosphorous acid at a molar ratio of 1:2.0:0.032, add BaO powder, antimony ethylene glycol, titanium dioxide and triphenyl phosphate and mix well Finally, the esterification reaction is carried out under pressure in a nitrogen atmosphere. The pressurized pressure is 0.2 MPa, and the temperature of the esterification reaction is 260 ° C. When the amount of water distilled in the esterification reaction reaches 95% of the theoretical value, it is an
Embodiment 3
[0068] A preparation method of a skin-core flame-retardant filament, the steps of which are as follows:
[0069] (1) Preparation of SiO 2 - BaO powder;
[0070] First heat the SiO 2 -BaO is kept at 400°C for 2.5 hours, then heated to 700°C, held for 1.5 hours, cooled in air, and finally crushed to obtain SiO with an average particle size of 0.48 microns 2 - BaO powder, SiO 2 -The content of BaO in BaO is 40wt%;
[0071] (2) prepare polyester;
[0072] (2.1) Esterification reaction;
[0073] Make a slurry of terephthalic acid, ethylene glycol and 2-carboxyethylphenylphosphorous acid at a molar ratio of 1:1.6:0.035, and add SiO 2 -After BaO powder, antimony acetate, titanium dioxide and trimethyl phosphite are mixed evenly, the esterification reaction is carried out under normal pressure in a nitrogen atmosphere. The temperature of the esterification reaction is 255 ° C. When the water in the esterification reaction is distilled When the amount reaches 92% of the theoretical
PUM
Property | Measurement | Unit |
---|---|---|
Particle size | aaaaa | aaaaa |
Breaking strength | aaaaa | aaaaa |
Breaking strength | aaaaa | aaaaa |
Abstract
Description
Claims
Application Information
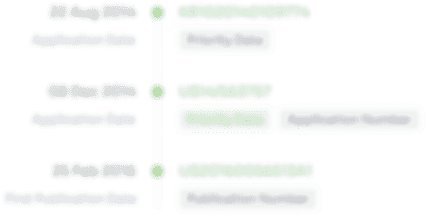
- R&D Engineer
- R&D Manager
- IP Professional
- Industry Leading Data Capabilities
- Powerful AI technology
- Patent DNA Extraction
Browse by: Latest US Patents, China's latest patents, Technical Efficacy Thesaurus, Application Domain, Technology Topic.
© 2024 PatSnap. All rights reserved.Legal|Privacy policy|Modern Slavery Act Transparency Statement|Sitemap