Carbon fiber precursor composition and method for preparing carbon fiber precursor
A precursor and carbon fiber technology, which is applied in the direction of single-component synthetic polymer rayon, fiber chemical characteristics, textiles and papermaking, etc., can solve problems such as difficult mass production, difficult removal of metal initiators or templates, and carbon fiber defects
- Summary
- Abstract
- Description
- Claims
- Application Information
AI Technical Summary
Benefits of technology
Problems solved by technology
Method used
Image
Examples
Embodiment 1
[0047] 100 parts by weight of acrylonitrile (acrylonitrile, available from Sigma-Aldrich), 7 parts by weight of methyl acrylate (methyl acrylate, available from Sigma-Aldrich), 0.645 parts by weight of itaconic acid (itaconic acid, available from Sigma-Aldrich) Aldrich), 0.107 parts by weight of azobisisobutyronitrile (N,N'-azobisisobutyronitrile, purchased from Sigma-Aldrich), and 0.268 parts by weight of ethylenediamine (1,2-diaminoethane) dissolved in 429.6 parts by weight of di Methyl sulfoxide (dimethylsulfoxide, purchased from Tedia) to obtain a solution. Nitrogen gas was passed into the above solution and stirred, then heated to 70°C for reaction. After reacting for 24 hours, the resultant was poured into methanol (methanol), wherein the weight ratio of the resultant to methanol was 1:3. Next, the precipitate was collected to obtain a polyacrylonitrile-methyl acrylate-itaconic acid copolymer (as a carbon fiber precursor). The carbon spectrum of the obtained copolymer was
Embodiment 2
[0049]100 parts by weight of acrylonitrile (acrylonitrile, available from Sigma-Aldrich), 7 parts by weight of methyl acrylate (methyl acrylate, available from Sigma-Aldrich), 0.645 parts by weight of itaconic acid (itaconic acid, available from Sigma-Aldrich) Aldrich), 0.107 parts by weight of azobisisobutyronitrile (N,N'-azobisisobutyronitrile, purchased from Sigma-Aldrich), and 0.535 parts by weight of 1,6-diaminohexane (1,6-diaminohexane, purchased from Sigma -Aldrich) was dissolved in 429.3 parts by weight of dimethylsulfoxide (dimethylsulfoxide, purchased from Tedia) to obtain a solution. Nitrogen gas was passed into the above solution and stirred, then heated to 70°C for reaction. After reacting for 24 hours, the resultant was poured into methanol (methanol), wherein the weight ratio of the resultant to methanol was 1:3. Next, the precipitate was collected to obtain a polyacrylonitrile-methyl acrylate-itaconic acid copolymer (as a carbon fiber precursor). The carbon spec
Embodiment 3
[0051] 100 parts by weight of acrylonitrile (acrylonitrile, available from Sigma-Aldrich), 7 parts by weight of methyl acrylate (methyl acrylate, available from Sigma-Aldrich), 0.645 parts by weight of itaconic acid (itaconic acid, available from Sigma-Aldrich) Aldrich), 0.107 parts by weight of azobisisobutyronitrile (N,N'-azobisisobutyronitrile, purchased from Sigma-Aldrich), and 0.268 parts by weight of deoxycholic acid (deoxycholic acid, purchased from Sigma-aldrich) dissolved in 429.6 parts by weight Parts of dimethyl sulfoxide (dimethylsulfoxide, purchased from Tedia) to obtain a solution. Nitrogen gas was passed into the above solution and stirred, then heated to 70°C for reaction. After reacting for 24 hours, the resultant was poured into methanol (methanol), wherein the weight ratio of the resultant to methanol was 1:3. Next, the precipitate was collected to obtain a polyacrylonitrile-methyl acrylate-itaconic acid copolymer (as a carbon fiber precursor). The carbon spe
PUM
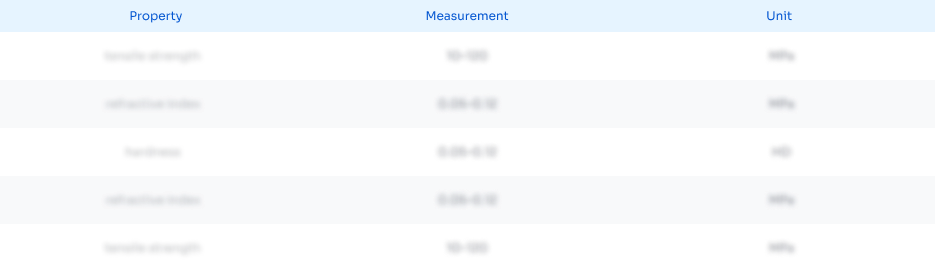
Abstract
Description
Claims
Application Information
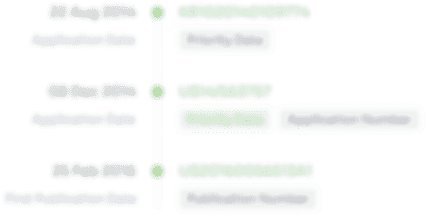
- R&D Engineer
- R&D Manager
- IP Professional
- Industry Leading Data Capabilities
- Powerful AI technology
- Patent DNA Extraction
Browse by: Latest US Patents, China's latest patents, Technical Efficacy Thesaurus, Application Domain, Technology Topic.
© 2024 PatSnap. All rights reserved.Legal|Privacy policy|Modern Slavery Act Transparency Statement|Sitemap