High-efficiency and energy-saving iron phosphate washing and dehydrating process
A technology of iron phosphate and process, which is applied in the direction of improving energy efficiency, improving process efficiency, chemical industry, etc., can solve the problems of long process flow, waste of materials, and many equipment, so as to save process flow, reduce production cost, and reduce energy consumption. consumption effect
- Summary
- Abstract
- Description
- Claims
- Application Information
AI Technical Summary
Problems solved by technology
Method used
Image
Examples
Example Embodiment
[0030] Example 1
[0031] This embodiment provides an efficient and energy-saving washing and dehydration process for iron phosphate, such as figure 1 , The specific process is as follows.
[0032] The iron phosphate slurry is fed into the filter press, filtered and then washed. The washing process is as follows: the tail gas of the heating section of the kiln passes through the 80℃ hot water of the steam separator and the 75℃ hot water is collected after the cooling section. To the hot water transfer tank, then transfer from the hot water transfer tank to the washing water tank, and then pump into the filter press for washing, washing until the washing liquid conductivity is less than 200μs / cm. After the filter press is washed, the exhaust gas of the kiln is passed through the steam-water separator to collect the dried 90℃ hot air to the air storage tank, from the air storage tank through the high pressure fan into the filter press for air drying operation, and the moisture content
Example Embodiment
[0035] Example 2
[0036] This embodiment provides an efficient and energy-saving washing and dehydration process for iron phosphate. The specific process is as follows.
[0037] The iron phosphate slurry is fed into the filter press, filtered in advance and then washed. The washing process is as follows: the tail gas of the heating section of the kiln passes through the 30℃ hot water of the steam separator and the 30℃ hot water after the cooling section is cooled. The hot water transfer tank is then transferred from the hot water transfer tank to the washing water tank, and then pumped into the filter press for washing until the washing liquid conductivity is less than or equal to 200μs / cm. After the filter press is washed, the exhaust gas from the kiln is passed through the steam-water separator and the dried 30℃ hot air is collected into the air storage tank. From the air storage tank, it is blown into the filter press through a high-pressure fan for air drying. The moisture cont
Example Embodiment
[0038] Example 3
[0039] This embodiment provides an efficient and energy-saving washing and dehydration process for iron phosphate, such as figure 1 , The specific process is as follows.
[0040] The iron phosphate slurry is fed into the filter press, filtered in advance and then washed. The washing process is as follows: the exhaust gas from the heating section of the kiln passes through the 90℃ hot water of the steam-water separator and the 90℃ hot water after the cooling section is cooled. The hot water transfer tank is then transferred from the hot water transfer tank to the washing water tank, and then pumped into the filter press for washing until the washing liquid conductivity is less than or equal to 200μs / cm. After the filter press is washed, the exhaust gas of the kiln is collected by the dried 120℃ hot air obtained by the steam-water separator to the air storage tank, and the air-drying operation is carried out through the high-pressure fan from the air storage tank to
PUM
Property | Measurement | Unit |
---|---|---|
Conductivity | aaaaa | aaaaa |
Abstract
Description
Claims
Application Information
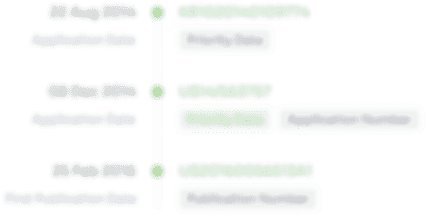
- R&D Engineer
- R&D Manager
- IP Professional
- Industry Leading Data Capabilities
- Powerful AI technology
- Patent DNA Extraction
Browse by: Latest US Patents, China's latest patents, Technical Efficacy Thesaurus, Application Domain, Technology Topic.
© 2024 PatSnap. All rights reserved.Legal|Privacy policy|Modern Slavery Act Transparency Statement|Sitemap