Method for preparing silicon-carbon composite material
A silicon-carbon composite material and mixed slurry technology, applied in nanotechnology, active material electrodes, electrical components, etc. for materials and surface science, can solve the problems of poor conductivity and obvious volume effect, and achieve increased conductivity, Reduce the specific surface area and improve the effect of the first pass effect
- Summary
- Abstract
- Description
- Claims
- Application Information
AI Technical Summary
Problems solved by technology
Method used
Image
Examples
preparation example Construction
[0030] The embodiment of the present invention provides a method for preparing a silicon-carbon composite material. The silicon-carbon composite material is prepared through two coating treatments, including the following steps:
[0031] S01. Preparation of nano silicon powder: providing micro silicon powder, a dispersant and a first organic solvent, adding the dispersant to the first organic solvent, adding the micro silicon powder after dispersion treatment to obtain a mixed slurry; Grinding the mixed slurry until D50 of silicon particles≤100nm to obtain slurry A;
[0032] S02. Surface coating treatment for the first time: provide the first binding agent, the second organic solvent and graphite, add the first binding agent in the second organic solvent, obtain solution B (bonding) after dispersion treatment agent solution); add the graphite in the solution B, mix and process to obtain a suspension C; add the suspension C to the slurry A, mix and spray dry to obtain a powder D;
Embodiment 1
[0063] A method for preparing silicon-based negative electrode material SiC, comprising the following steps:
[0064] S11. Preparation of nano silicon powder
[0065] 1) In a 15L container, add 900g of isopropanol, 100g of silicon powder, and 3g of sodium dodecylsulfonate in sequence, and stir for 30 minutes;
[0066]2) Add the above-mentioned slurry into a sand mill. The liner of the sand mill is made of zirconia and ground with 0.1mm zirconia balls until the silicon particle D50≤100nm to obtain slurry A.
[0067] S12. Primary surface coating
[0068] 1) Add 147g of phenolic resin to 2097g of isopropanol, stir for half an hour to obtain solution B, then add 233g of graphite to solution B, stir at high speed for half an hour to obtain suspension C;
[0069] 2) Add suspension C to slurry A, stir at high speed for half an hour, and then spray dry to obtain powder D;
[0070] 3) Treat under nitrogen gas at 500°C for 4 hours to obtain powder E.
[0071] S13. Secondary surface coa
Embodiment 2
[0076] A method for preparing silicon-based negative electrode material SiC, comprising the following steps:
[0077] S21. Preparation of nano silicon powder
[0078] 1) In a 15L container, sequentially add 900g of ethanol, 100g of silicon powder, and 3g of a copolymer of polycarboxylic acid derivatives, and stir for 30 minutes;
[0079] 2) Add the above-mentioned slurry into a sand mill. The liner of the sand mill is made of zirconia and ground with 0.1mm zirconia balls until the silicon particle D50≤100nm to obtain slurry A.
[0080] S22. Primary surface coating
[0081] 1) Add 147g of polyvinylpyrrolidone to 2097g of ethanol, stir for half an hour to obtain solution B, then add 233g of graphite to solution B, stir at high speed for half an hour to obtain suspension C;
[0082] 2) Add suspension C to slurry A, stir at high speed for half an hour, and then spray dry to obtain powder D;
[0083] 3) Treat under nitrogen gas at 500°C for 4 hours to obtain powder E.
[0084] S23
PUM
Property | Measurement | Unit |
---|---|---|
D50 | aaaaa | aaaaa |
Specific surface area | aaaaa | aaaaa |
D50 | aaaaa | aaaaa |
Abstract
Description
Claims
Application Information
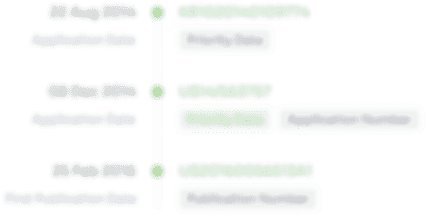
- R&D Engineer
- R&D Manager
- IP Professional
- Industry Leading Data Capabilities
- Powerful AI technology
- Patent DNA Extraction
Browse by: Latest US Patents, China's latest patents, Technical Efficacy Thesaurus, Application Domain, Technology Topic.
© 2024 PatSnap. All rights reserved.Legal|Privacy policy|Modern Slavery Act Transparency Statement|Sitemap