Roasting method for laterite-nickel ore pellets
A laterite nickel ore roasting technology, which is applied in the field of metallurgy, can solve the problem that the chlorination segregation process fails to realize large-scale treatment of laterite nickel ore industrial applications, reduce the partial pressure of the decomposition components of the chlorination agent, and incomplete chlorination segregation reactions, etc. problem, to achieve the effect of increasing production capacity, reducing production cost and increasing furnace temperature
- Summary
- Abstract
- Description
- Claims
- Application Information
AI Technical Summary
Problems solved by technology
Method used
Image
Examples
Embodiment 1
[0033] Such as figure 1 Shown, a kind of roasting method of laterite nickel ore pellet, comprises the steps:
[0034] 1) Feed the pellets obtained by the pellet preparation system 01 into the grate machine 02 for preheating, the temperature is controlled to be less than 400°C, and the preheated pellets are sent into the pellets by the bucket elevator 03 and the chain conveyor 04 Retort furnace 05.
[0035] 2) Feed the preheated pellets into the indirect heating tank furnace 05 for composite roasting. The calcination temperature is controlled at 900-1100° C., and the calcination reaction time is 30-90 minutes.
[0036] 3) The calcined sand balls roasted by the pot furnace enter the water jacket cooling box 06 to cool down to less than 200°C, and then are discharged by the discharge machine 07, and are supplied to the subsequent beneficiation operation to select nickel concentrate.
[0037] Such as Figure 3 to Figure 6 As shown, the structure of the retort furnace 05 used in t
Embodiment 2
[0044] Such as figure 2 Shown, a kind of roasting method of laterite nickel ore pellet, comprises the steps:
[0045] 1) Feed the pellets obtained by the pellet preparation system 01 into the grate machine 02 for preheating, the temperature is controlled to be less than 400°C, and the preheated pellets are sent into the pellets by the bucket elevator 03 and the chain conveyor 04 Retort furnace 05.
[0046] 2) Feed the preheated pellets into the indirect heating tank furnace 05 for composite roasting, the roasting temperature is controlled at 950-1050°C, and the roasting reaction time is 30-60 minutes.
[0047] 3) The calcined sand balls roasted by the pot furnace enter the water jacket cooling box 06 to cool down to less than 200°C, and then are discharged by the discharge machine 07, and are supplied to the subsequent beneficiation operation to select nickel concentrate.
[0048] The structure of the retort furnace 05 used in this embodiment is the same as that of the retort
PUM
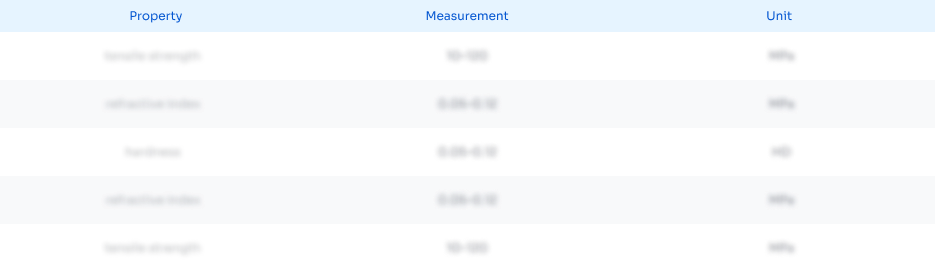
Abstract
Description
Claims
Application Information
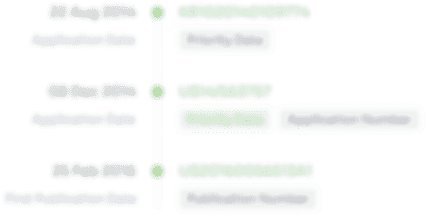
- R&D Engineer
- R&D Manager
- IP Professional
- Industry Leading Data Capabilities
- Powerful AI technology
- Patent DNA Extraction
Browse by: Latest US Patents, China's latest patents, Technical Efficacy Thesaurus, Application Domain, Technology Topic.
© 2024 PatSnap. All rights reserved.Legal|Privacy policy|Modern Slavery Act Transparency Statement|Sitemap