Self-heat balance laterite ore reduction method
一种自热平衡、红土矿的技术,应用在炉子类型、炉、竖炉等方向,能够解决规模小、工艺流程长、能量利用效率低等问题
- Summary
- Abstract
- Description
- Claims
- Application Information
AI Technical Summary
Problems solved by technology
Method used
Examples
Embodiment 1
[0036] Such as Figure 1-4 , the embodiment of the present invention provides a low-cost and suitable for laterite ore self-heat balance reduction shaft furnace direct reduction process, the reduction furnace adopts a shaft furnace, and the shaft furnace includes at least one reduction chamber 1, and each reduction chamber 1 consists of at least A combustion chamber 2 provides heat.
[0037] Described process comprises the following steps:
[0038]Raw material preparation steps: after drying the laterite ore with external water, the reducing agent is bituminous coal, in which the fixed carbon content is 65%-75% and the volatile matter content is 20%-35% by mass percentage. Among them, there is no requirement for the particle size distribution of coal and pellets, and the larger particle size needs to be crushed to be controlled within 30mm.
[0039] Distributing step: distributing the lump coal and the pellets into each of the reduction chambers 1, and in each of the reducti...
Embodiment 2
[0046] This embodiment provides a low-cost coal-based shaft furnace direct reduction process suitable for smelting laterite ore. The reduction furnace adopts a shaft furnace, and the shaft furnace includes at least one reduction chamber 1, and each reduction chamber 1 is composed of at least one Combustion chamber 2 heat supply;
[0047] Described process comprises the following steps:
[0048] Raw material preparation steps: mix the iron concentrate powder and the binder, and then pelletize on the disc pelletizer. The diameter of the pellets is about 20mm; In percentage terms, the fixed carbon content is 65% to 70%, and the volatile content is 30% to 35%;
[0049] Step of distributing materials: using furnace top feeding method, continuously and evenly distributing the pellets and lump coal into the reduction chamber 1 in layers and alternately; in each reduction chamber 1, the molar ratio of carbon to oxygen in the raw material is 1.1-1.2 ;
[0050] Direct reduction step:...
Embodiment 3
[0053] This embodiment provides a low-cost coal-based shaft furnace direct reduction process suitable for smelting laterite ore. The reduction furnace adopts a shaft furnace, and the shaft furnace includes at least one reduction chamber 1, and each reduction chamber 1 is composed of at least one Combustion chamber 2 heat supply;
[0054] Described process comprises the following steps:
[0055] Raw material preparation steps: mix the iron concentrate powder and the binder, and then pelletize on a disc pelletizer. The diameter of the pellets is 25mm; In terms of percentage, the fixed carbon content is 71%-75%, and the volatile matter content is 20%-28%.
[0056] Step of distributing materials: using furnace top charging method, continuously and evenly distributing the pellets and lump coal into the reduction chamber 1 in layers and alternately; in each reduction chamber 1, the molar ratio of carbon to oxygen in the raw material is 1.3-1.5 .
[0057] Direct reduction step: na...
PUM
Property | Measurement | Unit |
---|---|---|
particle diameter | aaaaa | aaaaa |
volatile fraction | aaaaa | aaaaa |
diameter | aaaaa | aaaaa |
Abstract
Description
Claims
Application Information
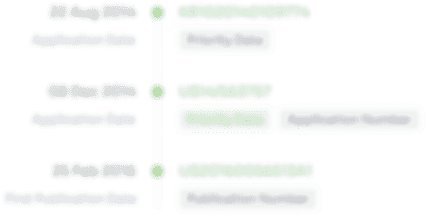
- R&D Engineer
- R&D Manager
- IP Professional
- Industry Leading Data Capabilities
- Powerful AI technology
- Patent DNA Extraction
Browse by: Latest US Patents, China's latest patents, Technical Efficacy Thesaurus, Application Domain, Technology Topic.
© 2024 PatSnap. All rights reserved.Legal|Privacy policy|Modern Slavery Act Transparency Statement|Sitemap