Method of preparing aluminum oxide-silicon carbide compound porous ceramic by aluminum-silicon industrial waste residues
A technology of industrial waste residue and porous ceramics, which is applied in the production and application of ceramic products and ceramic materials, can solve the problems of environmental pollution, inconvenience in daily life, and secondary pollution of the environment, and achieve low equipment requirements, significant economic benefits and environmental protection Benefit, the effect of appropriate porosity
- Summary
- Abstract
- Description
- Claims
- Application Information
AI Technical Summary
Problems solved by technology
Method used
Image
Examples
Embodiment 1
[0024] (1) Weigh 10g of fly ash and activated carbon mixed raw material, wherein the ratio of fly ash to activated carbon is 10:3; add 5% SiC and 3% phenolic resin by mass fraction; -1 Ball milling in a ball mill for 10 hours;
[0025] (2) Dry the raw material mixed by ball mill at 70° C. for 24 hours;
[0026] (3) After the drying is completed, pour the powder into the mold, and hold the pressure at 150MPa for 5 minutes to form;
[0027] (4) Then put the pressed ceramic body into a tubular resistance furnace, and introduce Ar gas; keep it at a preset temperature of 1500°C for 6h, control the temperature to 1000°C, and cool it with the furnace to obtain alumina-silicon carbide composite porous ceramics.
[0028] After testing, the porosity of the obtained porous ceramics is 64%, the compressive strength at room temperature is 12.7MPa, and the thermal diffusivity is 0.017cm 2 ·s -1 .
Embodiment 2
[0030] (1) Weigh 10g of fly ash and activated carbon mixed raw material, wherein the ratio of fly ash to activated carbon is 10:4; add 20% SiC and 3% phenolic resin; -1 Ball milling in a ball mill for 10 hours;
[0031] (2) Dry the raw material mixed by ball mill at 70° C. for 24 hours;
[0032] (3) After the drying is completed, pour the powder into the mold, and hold the pressure at 200MPa for 5 minutes to form;
[0033] (4) Then put the pressed ceramic body into a tubular resistance furnace, and introduce Ar gas; keep it at a preset temperature of 1600 °C for 4 hours, control the temperature to 1000 °C and cool it with the furnace to obtain alumina-silicon carbide composite porous ceramics.
[0034] After testing, the porosity of the obtained porous ceramics is 52%, the compressive strength at room temperature is 18.3MPa, and the thermal diffusivity is 0.021cm 2 ·s -1 .
Embodiment 3
[0036] (1) Weigh 10g of fly ash and activated carbon mixed raw material, wherein the ratio of fly ash to activated carbon is 10:5; add 10% SiC and 3% phenolic resin in mass fraction; -1 Ball milling in a ball mill for 10 hours;
[0037] (2) Dry the raw material mixed by ball mill at 70° C. for 24 hours;
[0038] (3) After the drying is completed, pour the powder into the mold, and hold the pressure at 100MPa for 5 minutes to form;
[0039] (4) Then put the pressed ceramic body into a beam-type resistance furnace and pass it with Ar gas, and keep it at a preset temperature of 1600°C for 6h, control the temperature to 1000°C and cool it with the furnace to obtain alumina-silicon carbide composite porous ceramics.
[0040] After testing, the porosity of the obtained porous ceramics is 60%, the compressive strength at room temperature is 13.4MPa, and the thermal diffusivity is 0.019cm 2 ·s -1 .
PUM
Property | Measurement | Unit |
---|---|---|
Compressive strength | aaaaa | aaaaa |
Compressive strength | aaaaa | aaaaa |
Compressive strength | aaaaa | aaaaa |
Abstract
Description
Claims
Application Information
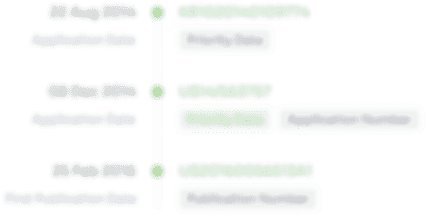
- R&D Engineer
- R&D Manager
- IP Professional
- Industry Leading Data Capabilities
- Powerful AI technology
- Patent DNA Extraction
Browse by: Latest US Patents, China's latest patents, Technical Efficacy Thesaurus, Application Domain, Technology Topic.
© 2024 PatSnap. All rights reserved.Legal|Privacy policy|Modern Slavery Act Transparency Statement|Sitemap