Laterite-nickel-ore reduction and cooling method
A technology of lateritic nickel ore and cooling method, which is applied in the field of metallurgy and material science, can solve the problems of ineffective utilization of reduced ore, unfavorable growth of iron grains, and increased grinding cost, so as to reduce subsequent grinding costs and increase nickel production. The recovery rate and the effect of lowering the reduction temperature
- Summary
- Abstract
- Description
- Claims
- Application Information
AI Technical Summary
Benefits of technology
Problems solved by technology
Method used
Image
Examples
Embodiment 1
[0037] A kind of laterite nickel ore reducing cooling method of the present invention comprises the following steps:
[0038] (1) Take 85wt% low-grade lateritic nickel ore containing 18.38% iron and 1.72% nickel, add 15wt% composite additives and mix in a mixer with a speed of 17r / min for 3 minutes, then add 10wt% water and continue mixing The mixture was obtained in 5 minutes, and the mixture was put into the feed box of a pair of roller presses, and pressed into agglomerates under a pressure of 60MPa. The composite additives include 15wt% water glass, 40wt% anthracite, 20wt% sodium humate and 25wt% limestone. The finished product rate of the dough is 81.35%, the drop strength is 95%, the compressive strength of the dough is 138N / piece, and the thermal burst index is 0.60%.
[0039] (2) In the raw agglomerate ore preheating system, use hot nitrogen to preheat the agglomerate to 900°C to obtain hot agglomerates. Put the hot agglomerate into the rotary kiln, and then reduce
Embodiment 2
[0043] A kind of laterite nickel ore reducing cooling method of the present invention comprises the following steps:
[0044](1) Take 80wt% low-grade lateritic nickel ore containing 18.38% iron and 1.72% nickel, add 20wt% composite additives and mix in a mixer with a speed of 17r / min for 3 minutes, then add 10wt% water and continue mixing The mixture was obtained in 5 minutes, and the mixture was put into the feed box of a pair of roller presses, and pressed into agglomerates under a pressure of 60MPa. The mixture is put into the feed box of the roller briquetting machine, and pressed into agglomerates under a pressure of 60MPa. The composite additives include 15wt% water glass, 40wt% anthracite, 20wt% sodium humate and 25wt% limestone. The finished product rate of the dough is 83.05%, the drop strength is 96%, the compressive strength of the dough is 149N / piece, and the thermal burst index is 0.40%.
[0045] (2) In the raw agglomerate preheating system, use hot nitrogen to
Embodiment 3
[0049] A kind of laterite nickel ore reducing cooling method of the present invention comprises the following steps:
[0050] (1) Take 85wt% low-grade lateritic nickel ore containing 18.38% iron and 1.72% nickel, add 15wt% composite additives and mix in a mixer with a speed of 17r / min for 3 minutes, then add 10wt% water, continue Mix for 5 minutes to obtain a mixture, put the mixture into the feed box of a pair of roller compactors, and press it into agglomerates under a pressure of 60MPa. The composite additives include 15wt% water glass, 40wt% anthracite, 20wt% sodium humate and 25wt% limestone. The finished product rate of the dough is 82.15%, the drop strength is 96%, the compressive strength of the dough is 142N / piece, and the thermal burst index is 0.50%.
[0051] (2) In the raw agglomerate preheating system, use hot nitrogen to preheat the raw agglomerates to 950°C to obtain hot agglomerates. Put the hot agglomerate into the rotary kiln, and then reduce it at 1250°C
PUM
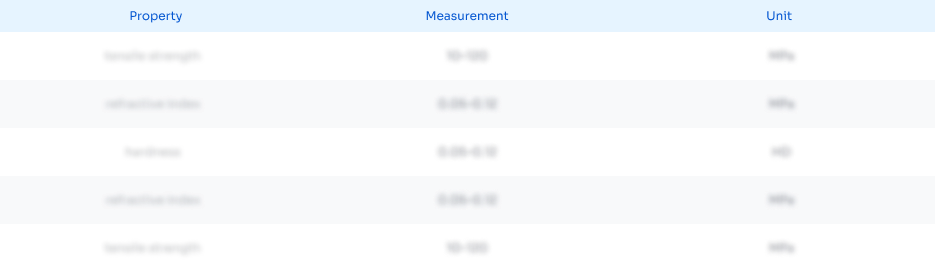
Abstract
Description
Claims
Application Information
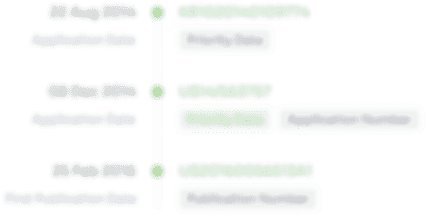
- R&D Engineer
- R&D Manager
- IP Professional
- Industry Leading Data Capabilities
- Powerful AI technology
- Patent DNA Extraction
Browse by: Latest US Patents, China's latest patents, Technical Efficacy Thesaurus, Application Domain, Technology Topic.
© 2024 PatSnap. All rights reserved.Legal|Privacy policy|Modern Slavery Act Transparency Statement|Sitemap