Refining slag and preparing method and application method of refining slag
An application method, the technology of refining slag, applied in the field of metallurgy, can solve the problems of affecting the composition of molten steel, not being able to form foamy slag in time, and increasing the oxygen content of molten steel with metal aluminum, and achieve the effect of high purity, good thermodynamic and dynamic conditions
- Summary
- Abstract
- Description
- Claims
- Application Information
AI Technical Summary
Problems solved by technology
Method used
Image
Examples
Embodiment
[0018] Embodiment: This embodiment specifically relates to a refining slag and its preparation and application method. The refining slag is processed and ground into powder by selecting calcite and alumina as raw materials, and then pressed into balls under high pressure to obtain a component distribution ratio of 52.7% of calcite powder ~72.7%, alumina powder 27.3%~47.3% refining slag, a certain amount of CO brought in by calcite during use 2, , quickly form foamy slag for submerged arc operation, and the formed foamy slag has high alkalinity and high purity, which provides good thermodynamic and kinetic conditions for desulfurization and deoxygenation of low-oxygen molten steel.
[0019] The components and mass percentages of the refining slag in this example are as follows: 52.7% to 72.7% of calcite powder, 27.3% to 47.3% of alumina powder, and the balance is impurities, wherein the CaCO in calcite powder 3 The content is greater than 99%, while the Al in alumina powder 2 o
PUM
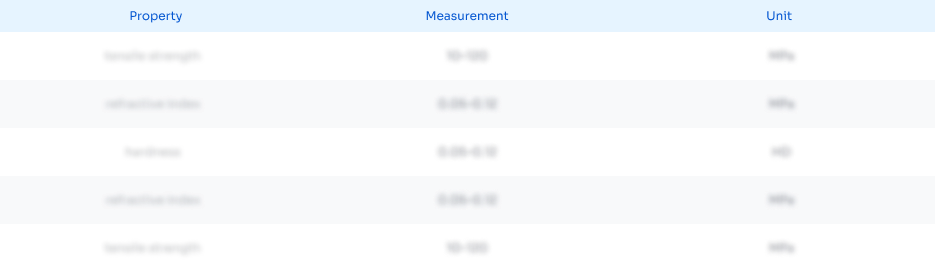
Abstract
Description
Claims
Application Information
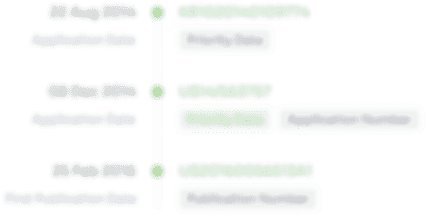
- R&D Engineer
- R&D Manager
- IP Professional
- Industry Leading Data Capabilities
- Powerful AI technology
- Patent DNA Extraction
Browse by: Latest US Patents, China's latest patents, Technical Efficacy Thesaurus, Application Domain, Technology Topic.
© 2024 PatSnap. All rights reserved.Legal|Privacy policy|Modern Slavery Act Transparency Statement|Sitemap