Camouflage plaque splitting and spraying method
A kind of plaque and camouflage technology, which is applied to coatings, devices that apply liquid to surfaces, special surfaces, etc., can solve problems such as robot jamming, improve efficiency, reduce empty running and path waste, and reduce path waste. Effect
- Summary
- Abstract
- Description
- Claims
- Application Information
AI Technical Summary
Problems solved by technology
Method used
Image
Examples
Embodiment 1
[0038] A typical embodiment of the present disclosure, such as figure 1 , figure 2 As shown, a kind of camouflage plaque splitting spraying method is provided, comprising the following steps:
[0039] Workpiece path scanning: scan all the spraying paths of the entire workpiece, detect all path lengths, and the path length information is used for re-planning of the path in the subsequent steps; of course, in this process, the position of the corresponding path can also be recorded to facilitate subsequent steps route re-planning;
[0040] Path planning parameter setting: compare all the path length information of the workpiece to be sprayed with the spraying limit range of the robot, and filter out the paths exceeding the spraying limit of the robot; combine the actual working conditions to set the distance value M of the transition point and the path split length Threshold L, the setting of M value and L value can make the path more reasonable and effective, among which the se
Embodiment 2
[0054] The present invention also provides another embodiment, which is different from Embodiment 1 in the path splitting process.
[0055] A method for splitting and spraying camouflage plaques, in which a working robot adopts fixed seven-axis spraying in the same area, including the following steps:
[0056] Workpiece path scanning, scan all the paths to be sprayed on the entire workpiece, detect all path lengths and store path length information;
[0057] Planning parameter setting, compare the length information of the workpiece’s spraying path with the robot’s spraying limit range, filter out the path beyond the robot’s spraying limit, and set the transition point distance value M and path split length according to the filtered path information Threshold L;
[0058] Spraying path splitting, splitting the filtered path, splitting the path exceeding the L value length into at least two continuous short paths whose length value is less than the L value, and adding Transition
PUM
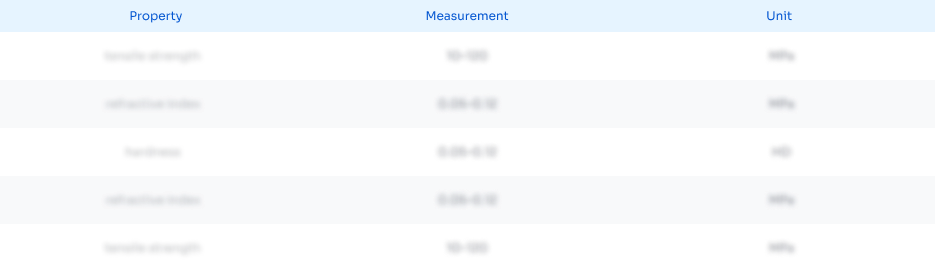
Abstract
Description
Claims
Application Information
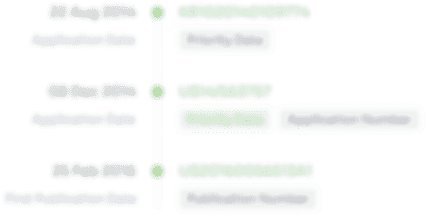
- R&D Engineer
- R&D Manager
- IP Professional
- Industry Leading Data Capabilities
- Powerful AI technology
- Patent DNA Extraction
Browse by: Latest US Patents, China's latest patents, Technical Efficacy Thesaurus, Application Domain, Technology Topic.
© 2024 PatSnap. All rights reserved.Legal|Privacy policy|Modern Slavery Act Transparency Statement|Sitemap