Abrasion resistant flexible composites and multilayer pipe liners for cured-in-place pipe
A composite material, multi-layer pipe technology, applied in chemical instruments and methods, synthetic resin layered products, layered products, etc., can solve the problems of transportation, wear, and inability to transport.
- Summary
- Abstract
- Description
- Claims
- Application Information
AI Technical Summary
Problems solved by technology
Method used
Image
Examples
example 1
[0145] The following were blended in a weight ratio of 50:15:35 to form the composition: ultra-high molecular weight ethylene-based polymer having a weight average molecular weight of 8,000,000 grams / mole, a density of 0.925 g / cc, and an intrinsic viscosity of 28 dL / g, and the average particle size D50 is 150μm (UTEC TM 6541, available from Braskem, Brazil); a polyethylene resin comprising a first molecular weight ethylene-based polymer component and a second molecular weight ethylene-based polymer component (DGDA-2420NT, density =0.940g / cc, high load melt index I 21 =9.5g / 10min, melt index I2 is 0.15g / 10min, and Mw / Mn is 9, available from U.S. Dow Chemical Company); and thermoplastic polyolefin elastomer (INFUSE TM 9010, ethylene / α-olefin interpolymer, density=0.877g / cc, melt index I2=0.5g / 10min, Mw / Mn is 2.6, available from Dow Chemical Company, USA). The composition was mixed with 600 ppm of fluoropolymer processing aid (melt flow index (265° C., 5 k
example 2
[0151] The following were blended in a weight ratio of 50:15:35 to form the composition: ultra-high molecular weight ethylene-based polymer having a weight average molecular weight of 8,000,000 grams / mole, a density of 0.925 g / cc, and an intrinsic viscosity of 28 dL / g, and the average particle size D50 is 150μm (UTEC TM6541, available from Brasco, Brazil); a polyethylene resin comprising a first molecular weight ethylene-based polymer component and a second molecular weight ethylene-based polymer component (DGDA-2420NT, density=0.940 g / cc , high load melt index I 21 =9.5g / 10min, melt index I2 is 0.15g / 10min, and Mw / Mn is 9, available from U.S. Dow Chemical Company); and thermoplastic polyolefin elastomer (ENGAGE TM 7387, ethylene / α-olefin interpolymer, density = 0.870 g / cc, melt index I2 = 0.5 g / 10 min, available from Dow Chemical Company, USA). The composition was mixed with 600 ppm of fluoropolymer processing aid (melt flow index (265° C., 5 kg) of 10 g
example 3
[0157] The following were blended in a weight ratio of 50:30:20 to form the composition: an ultra-high molecular weight ethylene-based polymer having a weight average molecular weight of 8,000,000 grams / mole, a density of 0.925 g / cc, and an intrinsic viscosity of 28 dL / g, and the average particle size D50 is 150μm (UTEC TM 6541, available from Brasco, Brazil); a polyethylene resin comprising a first molecular weight ethylene-based polymer component and a second molecular weight ethylene-based polymer component (DGDA-2420NT, density=0.940 g / cc , high load melt index I 21 =9.5g / 10min, melt index I2 is 0.15g / 10min, and Mw / Mn is 9, available from U.S. Dow Chemical Company); and thermoplastic polyolefin elastomer (INFUSE TM 9010, ethylene / α-olefin interpolymer, density = 0.877 g / cc, melt index I2 = 0.5 g / 10 min, available from Dow Chemical Company, USA). The composition was mixed with 600 ppm of fluoropolymer processing aid (melt flow index (265° C., 5 kg) at
PUM
Property | Measurement | Unit |
---|---|---|
Density | aaaaa | aaaaa |
Density | aaaaa | aaaaa |
Density | aaaaa | aaaaa |
Abstract
Description
Claims
Application Information
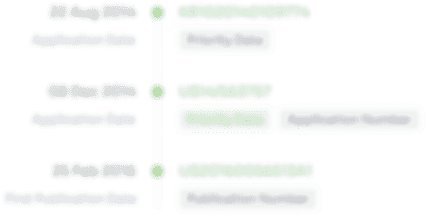
- R&D Engineer
- R&D Manager
- IP Professional
- Industry Leading Data Capabilities
- Powerful AI technology
- Patent DNA Extraction
Browse by: Latest US Patents, China's latest patents, Technical Efficacy Thesaurus, Application Domain, Technology Topic.
© 2024 PatSnap. All rights reserved.Legal|Privacy policy|Modern Slavery Act Transparency Statement|Sitemap