Preparation method of biomass derived carbon material
A technology of biomass and carbon materials, applied in chemical instruments and methods, carbon compounds, inorganic chemistry, etc., can solve problems such as low production efficiency and increased material production costs, and achieve the effects of reducing production costs and simplifying the preparation process
- Summary
- Abstract
- Description
- Claims
- Application Information
AI Technical Summary
Problems solved by technology
Method used
Examples
Embodiment 1
[0034] (1) Preparation of biomass-derived carbon materials
[0035] At room temperature, mix 5g of soybean protein isolate powder (Shansong Biotechnology, protein content ≥ 90%) with 5g of potassium hydroxide and 25g of water (mass ratio 1:1:5), and mechanically stir at 150r / min in a water bath at 85°C After 30 minutes, a colloidal semi-hydrolyzed product was formed, and then the colloidal semi-hydrolyzed product was dried in an oven at 100°C for 12 hours to obtain a dry hydrolyzed powder;
[0036] Mix 2 g of poplar wood powder with a particle size of 150 mesh, 1 g of dry hydrolyzed powder, and 2 g of zinc nitrate hexahydrate (mass ratio 1:0.5:1), stir at 60 r / min for 30 min, and transfer the resulting solid mixture into a tube furnace. Under the protection of nitrogen, the temperature was raised from room temperature to 900°C at a rate of 5°C / min, and high-temperature heat treatment was carried out at 900°C for 3 hours. During the heat treatment, zinc nitrate hexahydrate f
Embodiment 2
[0042] (1) Preparation of biomass-derived carbon materials
[0043] At room temperature, mix 5g of soybean protein isolate powder with 2.5g of sodium hydroxide and 20g of water (mass ratio 1:0.5:4), and mechanically stir at 200r / min in a 95°C water bath for 60min to form a colloidal semi-hydrolyzed product, and then the gelatinous The semi-hydrolyzed product was dried in an oven at 80°C for 24 hours to obtain a dry hydrolyzed powder;
[0044]Mix 2 g of poplar wood powder with a particle size of 150 mesh, 2 g of dry hydrolyzed powder, and 4 g of zinc nitrate hexahydrate (mass ratio 1:1:2), stir at 80 r / min for 20 min, and transfer the obtained solid mixture into a tube furnace. Under the protection of nitrogen, raise the temperature from room temperature to 1000°C at a rate of 3°C / min, and perform high-temperature heat treatment at 1000°C for 2 hours. During heat treatment, zinc nitrate hexahydrate first melts to form a liquid state and dissolves the dry hydrolyzed powder an
Embodiment 3
[0047] (1) Preparation of biomass-derived carbon materials
[0048] At room temperature, mix 5g of soybean protein isolate powder with 20g of potassium hydroxide and 40g of water (mass ratio 1:4:8), and mechanically stir at 300r / min in a 65°C water bath for 15min to form a colloidal semi-hydrolyzed product, and then the colloidal The semi-hydrolyzed product was dried in an oven at 90°C for 24 hours to obtain a dry hydrolyzed powder;
[0049] Mix 2 g of poplar wood powder with a particle size of 150 mesh, 4 g of dry hydrolyzed powder, and 6 g of zinc nitrate hexahydrate (mass ratio 1:2:3), stir at 100 r / min for 30 min, and transfer the resulting solid mixture into a tube furnace. Under the protection of nitrogen, the temperature was raised from room temperature to 800°C at a rate of 4°C / min, and high-temperature heat treatment was carried out at 800°C for 5 hours. During the heat treatment, zinc nitrate hexahydrate first melted to form a liquid state, and the dry hydrolyzed
PUM
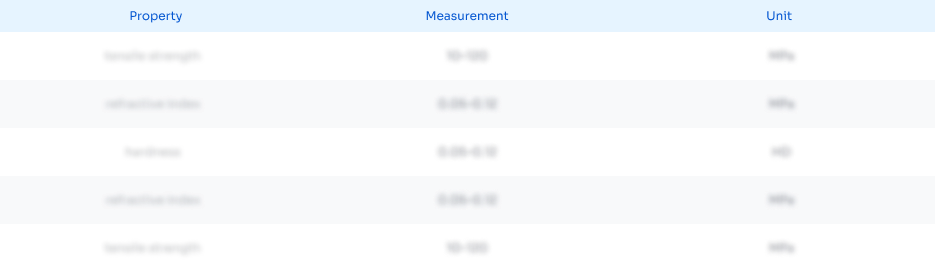
Abstract
Description
Claims
Application Information
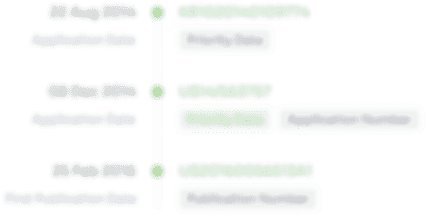
- R&D Engineer
- R&D Manager
- IP Professional
- Industry Leading Data Capabilities
- Powerful AI technology
- Patent DNA Extraction
Browse by: Latest US Patents, China's latest patents, Technical Efficacy Thesaurus, Application Domain, Technology Topic.
© 2024 PatSnap. All rights reserved.Legal|Privacy policy|Modern Slavery Act Transparency Statement|Sitemap