Preparation method of high-resistance flaky soft magnetic powder
A soft magnetic powder, high resistance technology, used in permanent magnet manufacturing, inductor/transformer/magnet manufacturing, circuits, etc., can solve the problem of increasing the cost of powder surface treatment, large diameter-to-thickness ratio of flake powder, and poor surface treatment effect. and other problems, to achieve the effect of promoting sufficient and uniform adsorption, increasing the area, and high environmental friendliness.
- Summary
- Abstract
- Description
- Claims
- Application Information
AI Technical Summary
Problems solved by technology
Method used
Image
Examples
Embodiment 1
[0040] In this example, the equipment used to prepare high-resistance flake-shaped soft magnetic powder is improved on the basis of the existing tube furnace. The furnace 1-1 of the equipment is made of corundum, and the whole is in the shape of a slender hollow cylinder. , the furnace 1-1 is arranged according to its axial direction parallel to the vertical direction (the direction of the gravity of the object), the bottom of the furnace 1-1 is dense, and the gas nozzle 1-3 is connected to the bottom of the furnace 1-1, Except for the access of the gas nozzle 1-3, the bottom of the furnace 1-1 is a compact structure, and the top of the furnace 1-1 is an open structure that communicates with the outside world, and the flange 1-1 that matches the open structure 4 Cover the top of the furnace 1-1. Such as figure 1 As shown, along the axial direction of the furnace 1-1, from bottom to top, the reaction area in the furnace 1-1 is divided into the first acceleration area 1-11, the ma
Embodiment 2
[0051] In this embodiment, the equipment used to prepare high-resistance flake-shaped soft magnetic powder is improved on the basis of the existing tube furnace. The furnace 2-1 of the equipment is made of corundum, and the whole is in the shape of a slender hollow cylinder. , with a hollow cylindrical inner cavity as the reaction area 2-11, the furnace 2-1 is arranged according to its axial direction parallel to the horizontal direction, and both ends of the furnace 2-1 are open structures that communicate with the outside world, respectively with the open Flanges 2-3 matching the mouth structure cover the two ends of the furnace 2-1. Such as figure 2 As shown, two parallel metal pole plates 2-2 are arranged around the side wall of the furnace 2-1 corresponding to the reaction area 2-11, and the metal pole plates 2-2 are connected to alternating current to generate An alternating magnetic field with uniform spatial distribution and periodic changes in size with time. At the sa
Embodiment 3
[0060] In this embodiment, the equipment used to prepare high-resistance sheet-shaped soft magnetic powder is improved on the basis of the existing tube furnace. The furnace 3-1 of the equipment is made of corundum, and the whole is in the shape of a slender hollow cylinder. , with a hollow cylindrical inner cavity as the reaction area 3-11, the furnace 3-1 is arranged according to its axial direction parallel to the horizontal direction, and both ends of the furnace 3-1 are open structures that communicate with the outside world. Flanges 3-3 matching the mouth structure cover the two ends of the furnace 3-1. Such as image 3 As shown, a spiral stirring paddle 3-2 extending into the reaction zone 3-11 is also installed at one end of the furnace 3-1. connect.
[0061] In this embodiment, air is used to provide an oxidizing atmosphere, and a set of treatment groups is set, marked as treatment group III. The specific operations for group III are as follows:
[0062] S1. Sample i
PUM
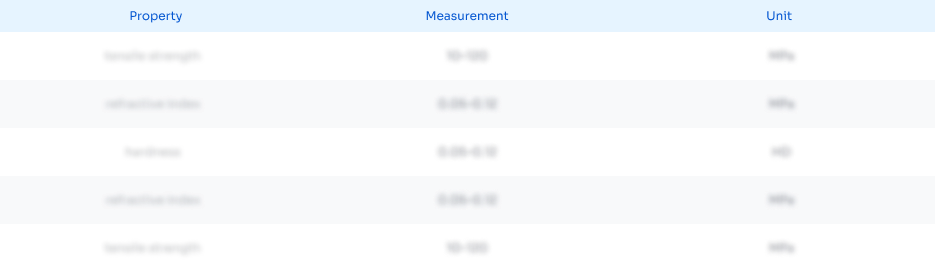
Abstract
Description
Claims
Application Information
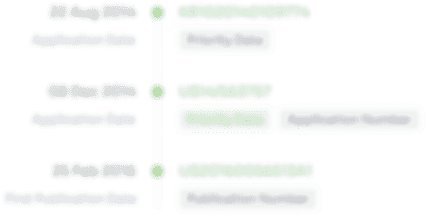
- R&D Engineer
- R&D Manager
- IP Professional
- Industry Leading Data Capabilities
- Powerful AI technology
- Patent DNA Extraction
Browse by: Latest US Patents, China's latest patents, Technical Efficacy Thesaurus, Application Domain, Technology Topic.
© 2024 PatSnap. All rights reserved.Legal|Privacy policy|Modern Slavery Act Transparency Statement|Sitemap