Micromechanical structure driving amplitude correction system and method
A micro-mechanical structure and amplitude correction technology, which is applied in the field of micro-electromechanical systems, can solve problems such as different capacitance change rates of micro-mechanical structures, different mechanical drive amplitudes of different devices, and differences in key dimensions, so as to correct electrical measurement errors and measure resonant frequency simply. , improve the effect of consistency
- Summary
- Abstract
- Description
- Claims
- Application Information
AI Technical Summary
Problems solved by technology
Method used
Examples
Example Embodiment
[0031] Example one
[0032] figure 1 Shows a schematic diagram of the system framework of an embodiment of the present invention, which includes movable mass 100, spring beams 101 to 104, movable comb teeth 111 and 112, fixed comb teeth 121 and 122, fixed anchor points 130 to 132, The C / V converter 142, the amplitude reading module 143, the frequency reading module 144, the amplitude correction module 145, and the automatic gain module 146.
[0033] The movable mass fast 100 is connected to the fixed anchor point 130 through the spring beams 101 to 104 to form a resonance system. The spring beams 101 to 104 are arranged along the X direction (the horizontal direction in the viewing angle of the figure), so that the mass 100 can be in the Y direction (The vertical direction of the viewing angle of the figure) is active, and further can vibrate at a specific frequency in the Y direction. The theoretical resonance frequency is:
[0034]
[0035] In the formula, m is the mass of the mass
Example Embodiment
[0057] Example two
[0058] In the first embodiment, the amplitude readout module 143 and the frequency readout module 144 simultaneously receive the output of the C / V converter 142 to correct the driving amplitude in real time. In practical applications, the resonance of the micromechanical structure under a stable external environment The frequency is very stable and basically does not change with time.
[0059] Therefore, in this embodiment, Image 6 As shown, based on the first embodiment, a switch 147 is provided between the C / V converter 142 and the frequency reading module 144. In application, the setting switch 147 can only be closed when calibrating or calibrating the micromechanical structure or the sensor adopting the corresponding micromechanical structure. When the switch 147 is opened, the frequency readout module 144 will set the frequency of the previously read signal to a fixed value Write to the amplitude correction module 145 in a manner. The effect of this is
Example Embodiment
[0060] Example three
[0061] In the first and second embodiments, in order to make the driving force approximate to simple harmonic force, the amplitude of the DC voltage applied to the mass 100 needs to be much larger than the amplitude of the AC voltage applied to the driving capacitor, in order to adapt to the more general Situation, in this embodiment, such as Figure 7 As shown, two sides of the mass 100 are symmetrically provided with a fixed anchor point 231 and a fixed anchor point 232, as well as a fixed anchor point 234 and a fixed anchor point 233.
[0062] The fixed anchor point 231 is provided with fixed comb teeth 221, and the fixed comb teeth 221 cooperate with a part of the movable comb teeth 111 to form a first driving capacitor. Correspondingly, a fixed comb tooth 222 is provided on the fixed anchor point 232, and the fixed comb tooth 222 cooperates with a part of the movable comb tooth 112 to form a second driving capacitor. The driving excitation output by the au
PUM
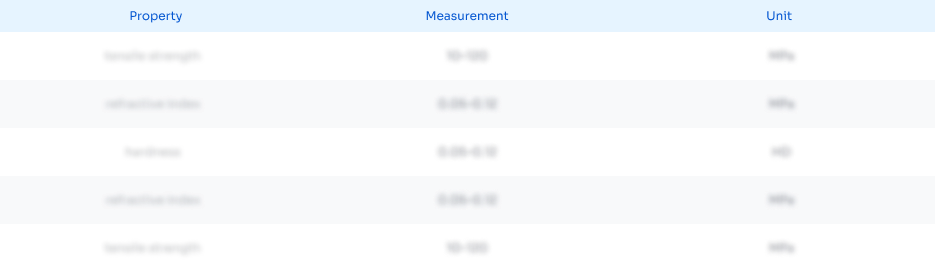
Abstract
Description
Claims
Application Information
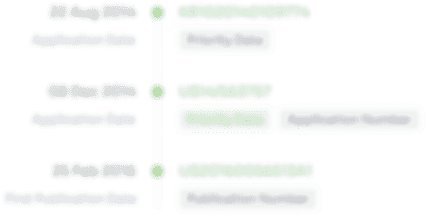
- R&D Engineer
- R&D Manager
- IP Professional
- Industry Leading Data Capabilities
- Powerful AI technology
- Patent DNA Extraction
Browse by: Latest US Patents, China's latest patents, Technical Efficacy Thesaurus, Application Domain, Technology Topic.
© 2024 PatSnap. All rights reserved.Legal|Privacy policy|Modern Slavery Act Transparency Statement|Sitemap