Method of hardening tool edge through soldering wire and tool edge fixture
A knife edge and knife technology, applied in the field of knife edge hardening treatment method and the jig used to realize the above method, can solve the problems of increasing the price of the knife, the requirement of management environment, and the expensive cost of cladding powder, etc.
- Summary
- Abstract
- Description
- Claims
- Application Information
AI Technical Summary
Problems solved by technology
Method used
Image
Examples
Embodiment Construction
[0027] Combine below Figure 1-9 The present invention will be further described with specific embodiments.
[0028] See attached figure 1 , which is a schematic diagram of the structure used in the powder edge hardening method in the prior art. It can be seen that in order to realize hardening treatment on both sides of the blade during the processing, the knife to be processed needs to be placed upright, that is, the tool processing process In all vertical machining, due to the arc structure of the tool blade, it is necessary to consider the transformation of the Z-axis height in the machining path programming, resulting in complicated machining; and because the machining method is point machining, it needs to be clad back and forth many times to achieve For the processing of a single knife, in order to ensure the processing quality, it is necessary to precisely control multiple working parameters such as laser power, laser focal length, powder output, shielding gas volume, m
PUM
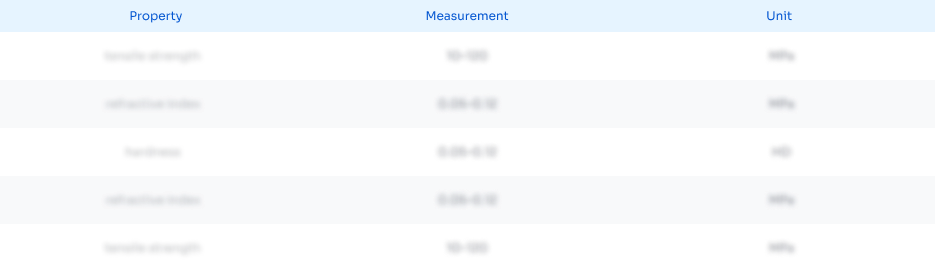
Abstract
Description
Claims
Application Information
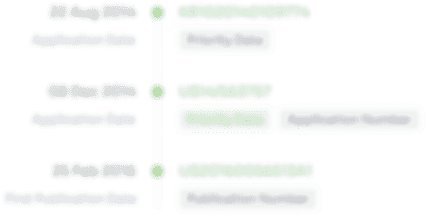
- R&D Engineer
- R&D Manager
- IP Professional
- Industry Leading Data Capabilities
- Powerful AI technology
- Patent DNA Extraction
Browse by: Latest US Patents, China's latest patents, Technical Efficacy Thesaurus, Application Domain, Technology Topic.
© 2024 PatSnap. All rights reserved.Legal|Privacy policy|Modern Slavery Act Transparency Statement|Sitemap