Preparation method of titanium dioxide primary product with improved light resistance
A technology of titanium dioxide and light resistance, applied in the direction of titanium dioxide, titanium oxide/hydroxide, etc., can solve the problem of low light resistance of the first titanium dioxide product, improve the electronic work function, improve the service life, and uniform particle size distribution Effect
- Summary
- Abstract
- Description
- Claims
- Application Information
AI Technical Summary
Problems solved by technology
Method used
Image
Examples
preparation example Construction
[0019] The preparation method of the high light fastness titanium dioxide of the present invention can specifically be carried out as follows:
[0020] (1) Add second-washed metatitanic acid into deionized water or distilled water, perform beating and dispersion treatment, and obtain metatitanic acid slurry with a slurry concentration of 300-600g / L;
[0021] (2) Add calcined seed crystals, vanadium compounds, carbon powder, potassium compounds, phosphorus compounds, and aluminum compounds to the slurry obtained in step (1), and stir for 30 to 90 minutes to obtain slurry; the amount of vanadium added is 0.01 to 0.3 wt%, the amount of carbon powder added is 0.05-0.6wt%;
[0022] (3) Put the slurry obtained in step (2) into an oven, and dry it at 60-120°C;
[0023] (4) Put the material obtained in step (3) into a program-controlled muffle furnace, and the heating rate is 50-150° C. / min;
[0024] (5) When the temperature rises to 150-250°C, keep it warm for 60-180 minutes to de
Embodiment 1
[0036] (1) Add second-washed metatitanic acid to deionized water or distilled water, and perform beating and dispersion treatment to obtain metatitanic acid slurry with a slurry concentration of 300g / L;
[0037] (2) Add the calcined seed crystal, potassium compound, phosphorus compound, and aluminum compound to the metatitanic acid slurry, and stir for 45 minutes each time a substance is added to obtain the slurry;
[0038] (3) adding 0.05% wt of vanadium compound and 0.10% wt of carbon powder to the slurry obtained in step (2);
[0039] (4) Dry the material obtained in step (3), and then put it into a program-controlled muffle furnace. When the temperature rises to 200°C, keep it warm for 120 minutes to dehydrate the material, and then continue to heat up at a rate of 50°C / min. When the temperature rises to 600°C / min, keep it warm for 60 minutes to desulfurize the material, then continue to heat up, and at the same time introduce oxygen at a heating rate of 120°C / min, wh
Embodiment 2
[0043] (1) Add second-washed metatitanic acid to deionized water or distilled water, and perform beating and dispersion treatment to obtain metatitanic acid slurry with a slurry concentration of 300g / L;
[0044] (2) Add the calcined seed crystal, potassium compound, phosphorus compound, and aluminum compound to the metatitanic acid slurry, and stir for 45 minutes each time a substance is added to obtain the slurry;
[0045] (3) adding 0.15%wt of vanadium compound and 0.25%wt of carbon powder to the slurry obtained in step (2);
[0046] (4) Dry the material obtained in step (3), put it into a program-controlled muffle furnace, and heat up at a rate of 60°C / min. When the temperature rises to 200°C, keep it warm for 120min to dehydrate the material, and then continue to heat up. The rate is 100°C / min. When the temperature rises to 600°C / min, keep it warm for 60 minutes to desulfurize the material, then continue to heat up, and at the same time feed oxygen. The heating rate i
PUM
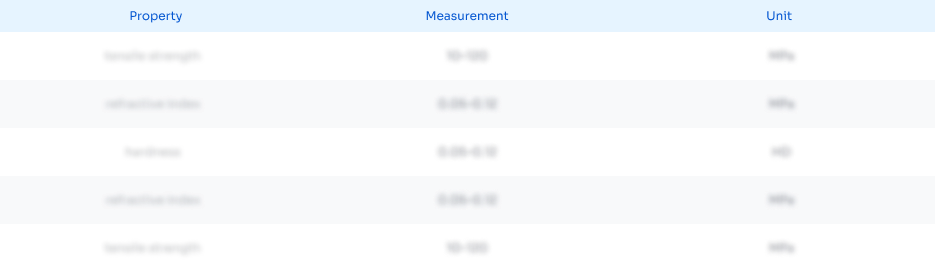
Abstract
Description
Claims
Application Information
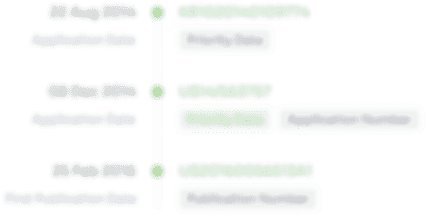
- R&D Engineer
- R&D Manager
- IP Professional
- Industry Leading Data Capabilities
- Powerful AI technology
- Patent DNA Extraction
Browse by: Latest US Patents, China's latest patents, Technical Efficacy Thesaurus, Application Domain, Technology Topic.
© 2024 PatSnap. All rights reserved.Legal|Privacy policy|Modern Slavery Act Transparency Statement|Sitemap