Low-aluminum and low-silicon welding wire steel low-sulfur-control smelting method
A smelting method and welding wire steel technology, which is applied in the smelting field of low-aluminum and low-silicon welding wire steel to control low sulfur content, can solve the problems such as the inability to stably control the low-sulfur content of welding wire steel, and achieve the goals of reducing deoxidation products, controlling stability, and reducing oxidation Effect
- Summary
- Abstract
- Description
- Claims
- Application Information
AI Technical Summary
Benefits of technology
Problems solved by technology
Method used
Examples
Embodiment 1
[0019] For the smelting of molten iron ≥ 74t tons, the sulfur content of the molten iron is 0.023%, the amount of tapping is controlled at 102 tons, to prevent slag, 25 tons of steel is left in the electric furnace, and the slag is prevented from rolling in the tapping furnace, and alloying is performed after the electric furnace steelmaking is completed. The process is to add 150kg / t of aluminum pellets for deoxidation, add 350kg / t of metal manganese to adjust the composition, add 300kg / t of lime; stir for 3 minutes after tapping from the electric furnace, oxidize the slag after stirring, dump the slag and hang it back to the refining furnace; Furnace, add 600kg of active lime and 300kg of fluorite, add in 3 batches, power chemical slag refining, stir argon flow rate 250Nl / min, add 60kg of aluminum wire for diffusion deoxidation, refine for 15min, add 250kg of active lime and 100kg of fluorite, Use 100kg of deoxidizing slagging agent to continue diffusion deoxidation, sam
Embodiment 2
[0021] For the smelting of molten iron ≥ 72 tons, the sulfur content of the molten iron is 0.022%, the amount of tapping is controlled at 100 tons, to prevent slag, 20 tons of steel is left in the electric furnace, and the slag is prevented from rolling in the tapping furnace, and alloying is carried out after the electric furnace steelmaking is completed The process is to add 1.4kg / t of aluminum pellets for deoxidation, add 3.3kg / t of manganese to adjust the composition, add 2.5kg / t of lime; stir for 2.5 minutes after tapping from the electric furnace, oxidize the slag after stirring, dump the slag and hang it back to the refining furnace; Put it in the refining furnace, add active lime 5.8kg / t and fluorite 2.6kg / t, add in 3 batches, power chemical slag refining, stir argon flow rate 230Nl / min, add aluminum wire 0.55kg / t diffusion deoxidation, refining 12 minutes, add active lime 2.3kg / t and fluorite 0.7kg / t, use deoxidation slagging agent 0.9kg / t to continue
Embodiment 3
[0023] For the smelting of molten iron ≥ 70t tons, the sulfur content of the molten iron must be 0.020%, the amount of steel tapping should be controlled at 98 tons to prevent slag, and 15 tons of steel should be left in the electric furnace to prevent slag rolling in the tapping furnace. The process of melting is to add 130kg of aluminum pellets for deoxidation, add 300kg of manganese to adjust the composition, add 200kg / t of lime; stir for 2 minutes after tapping out of the electric furnace, pour out the oxide slag, and hang it back to the refining furnace after pouring out the slag; put it in the refining furnace, add 550kg of active lime and 200kg of fluorite are added in 2 batches, powered by chemical slag for refining, argon gas flow is stirred at 200Nl / min, 50kg of aluminum wire is added for diffusion deoxidation, refining is performed for 10min, and 150kg of active lime and 50kg of fluorite are added. 80kg of slag agent continues to diffuse and deoxidize, sampling and
PUM
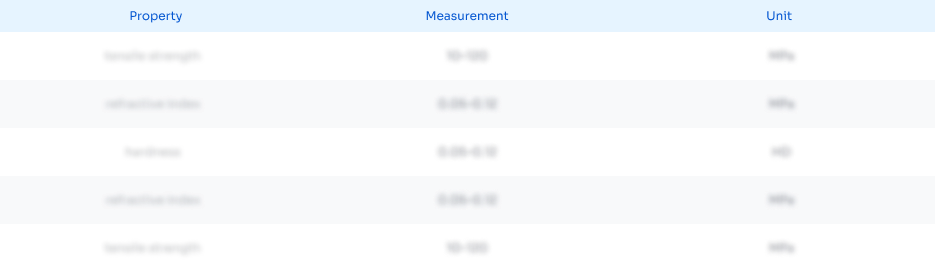
Abstract
Description
Claims
Application Information
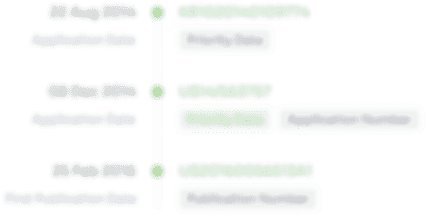
- R&D Engineer
- R&D Manager
- IP Professional
- Industry Leading Data Capabilities
- Powerful AI technology
- Patent DNA Extraction
Browse by: Latest US Patents, China's latest patents, Technical Efficacy Thesaurus, Application Domain, Technology Topic.
© 2024 PatSnap. All rights reserved.Legal|Privacy policy|Modern Slavery Act Transparency Statement|Sitemap