Polyurethane resin for winding process, resin/fiber composite material as well as preparation method and application of resin/fiber composite material
A fiber composite material and polyurethane resin technology, which is applied in the fields of resin synthesis and composite material preparation, can solve the problems of polyurethane resin such as short operation time, environmental protection and mechanical performance defects, so as to prolong the operation time, improve flexibility, and cheap raw materials Effect
- Summary
- Abstract
- Description
- Claims
- Application Information
AI Technical Summary
Benefits of technology
Problems solved by technology
Method used
Image
Examples
Embodiment 1
[0043] Step 1: Warm up 1580g of ethylene glycol diglycidyl ether to 120°C to remove water by vacuuming for 1 hour. At 80°C, add 600g of acetic acid and 16g of triphenyl in accordance with the molar ratio of epoxy and carboxyl groups of 2:1 phosphine catalyst, reacted for 4 hours to obtain a compound containing hydroxyl and epoxy groups simultaneously, according to the ratio of isocyanate group and hydroxyl molar ratio of 1:1, add 1250g 2,4-diphenylmethane diisocyanate and 4, 4-Diphenylmethane diisocyanate mixture (any ratio is acceptable), continue to react for 6 hours to obtain epoxy group-terminated carbamate mixture.
[0044] Step 2: Configure the curing agent according to the following components and weight percentages:
[0045] High molecular weight amino-terminated polyether 30%, n=30
[0046] Low molecular weight amino-terminated polyether 60%, n=1
[0047] IPDA 10%
[0048] Oxazolidine water remover (ALT-101, Hunan Anxiang Elite Chemical Co., Ltd.) 1%
[0049] Fluorin
Embodiment 2
[0054] Step 1: Heat 2020g of butanediol diglycidyl ether to 120°C to remove water by vacuuming for 1 hour. At 140°C, add 740g of propionic acid and 2.76g P-toluenesulfonic acid catalyst, reacted for 0.5 hours to obtain a compound containing hydroxyl and epoxy groups at the same time, according to the ratio of isocyanate group and hydroxyl molar ratio of 1:1, add 1335g of polymerized diphenylmethane diisocyanate (commonly known as black material) at room temperature ), the reaction was continued for 10 hours to obtain an epoxy-terminated carbamate mixture.
[0055] Step 2: Configure the curing agent according to the following components and weight percentages:
[0056] High molecular weight amino-terminated polyether 10%, n=10
[0057] Low molecular weight amino-terminated polyether 60%, n=6
[0058] IPDA 20%
[0059] Triester orthoformate water remover (Bailingwei Company) 2%
[0060] Fluorine defoamer (MTK-4352, Nantong Matech New Material Co., Ltd.) 2%.
[0061] Step 3, mi
Embodiment 3
[0065] Step 1: Heat 2300g of hexanediol diglycidyl ether to 120°C to remove water by vacuuming for 1 hour. At 120°C, add 880g of butyric acid and 15.9g Triethylamine catalyst, reacted for 2 hours, obtained the compound containing hydroxyl group and epoxy group simultaneously, according to the ratio of isocyanate group and hydroxyl molar ratio being 1:1, add 1104.5g polymerization diphenylmethane diisocyanate (667g) and A mixture of methylphenyl diisocyanates (437.5 g) was continued for 8 hours to give a mixture of epoxy-terminated urethanes.
[0066] Step 2: Configure the curing agent according to the following components and weight percentages:
[0067] High molecular weight amino-terminated polyether 30%, n=20
[0068] Low molecular weight amino-terminated polyether 20%, n=4
[0069] HMDA 20%
[0070] Carbodiimide water remover (DMAP, Bailingwei Company) 2%
[0071] Fluorine defoamer (MTK-4352, Nantong Matech New Material Co., Ltd.) 1.5%
[0072] Step 3: Mix the epoxy resi
PUM
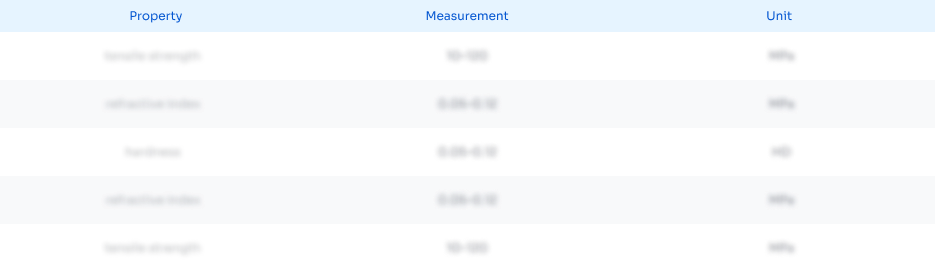
Abstract
Description
Claims
Application Information
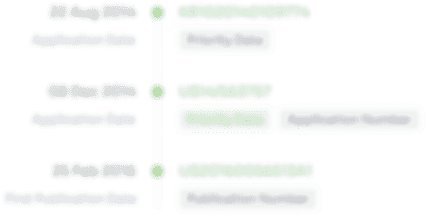
- R&D Engineer
- R&D Manager
- IP Professional
- Industry Leading Data Capabilities
- Powerful AI technology
- Patent DNA Extraction
Browse by: Latest US Patents, China's latest patents, Technical Efficacy Thesaurus, Application Domain, Technology Topic.
© 2024 PatSnap. All rights reserved.Legal|Privacy policy|Modern Slavery Act Transparency Statement|Sitemap