Method for avoiding drilling abnormity of rigid-flex board
A soft-rigid combination board, abnormal technology, applied in electrical components, printed circuit manufacturing, printed circuit and other directions, can solve the problems of dry film debris residue, bottom hole crater abnormality, electroplating hole abnormality and other problems, to reduce production costs, The effect of improving production yield
- Summary
- Abstract
- Description
- Claims
- Application Information
AI Technical Summary
Problems solved by technology
Method used
Examples
Example Embodiment
[0013]The present invention provides a method for avoiding abnormal drilling of a rigid-flex board, which includes the following steps:
[0014]S1. According to the expansion and contraction ratio of the soft-hard board, prepare a mat plank and drill two positioning holes on the mat plank;
[0015]S2. The project produces LDI exposure data based on the height difference area on the back of the soft and hard board, and exposes the area that needs to be filled;
[0016]S3. Paste dry film on the front of the mat wood, LDI grabs two drill positioning holes for exposure, and exposes according to the engineering data;
[0017]S4. Remove the dry film from the unwanted area on the front of the mat board by developing, leaving the dry film on the mat board in the area that needs to be filled;
[0018]S5. Put the dry film-filled wooden board on the PIN nail, and then put the soft and hard board on the PIN nail, and use the dry film on the front of the wooden board to fill the hollow area of the soft and hard
PUM
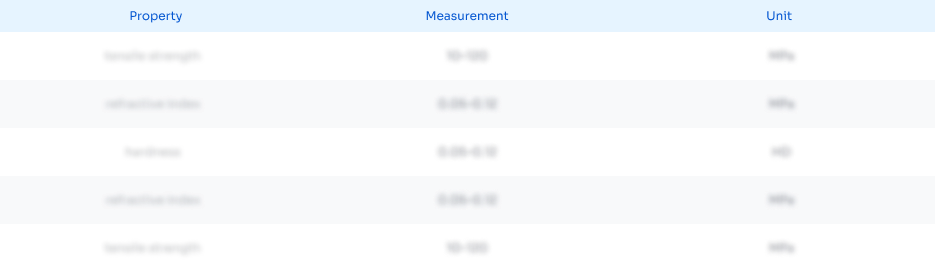
Abstract
Description
Claims
Application Information
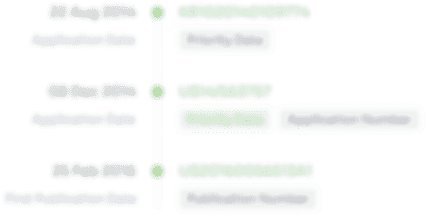
- R&D Engineer
- R&D Manager
- IP Professional
- Industry Leading Data Capabilities
- Powerful AI technology
- Patent DNA Extraction
Browse by: Latest US Patents, China's latest patents, Technical Efficacy Thesaurus, Application Domain, Technology Topic.
© 2024 PatSnap. All rights reserved.Legal|Privacy policy|Modern Slavery Act Transparency Statement|Sitemap